随着科学技术水平发展,对材料的需求逐渐升高,单一的金属或陶瓷材料已很难完全满足其对材料综合性能的要求,材料的复合化已成为必然趋势。陶瓷金属复合材料继承了陶瓷材料的高比刚度和金属材料的高韧性等优点,大大拓宽了该类复合材料的研究和应用领域。复合材料的性能主要取决于各组元的性能、体积分数、增强相的分布和尺寸以及基体增强相的界面结合情况等因素。陶瓷金属复合材料显微组织形态不同,其动态力学性能有很大差异。通过对显微组织的改善可以大幅度提高复合材料在高应变率服役条件下的性能。因此,通过对复合材料的微观失效机理研究,揭示复合材料显微组织特征参数对其动态力学性能影响规律,显得尤为重要。
首页 >> 学术研究 >> 陶瓷金属复合材料微观力学响应行为
陶瓷金属复合材料微观力学响应行为
文献1(2014):Simulation of damage and failure processes of interpenetrating SiC/Al composites subjected to dynamic compressive loading(动态压缩载荷作用下SiC/Al双连通复合材料损伤破坏过程仿真)
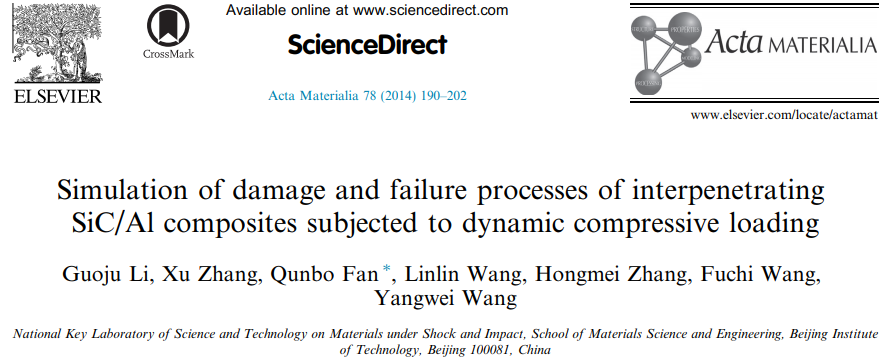
The crack initiation is generated both on the up and down sides of the SiC phase at t = 2.4μs. Subsequently, the two cracks penetrate into the inner side of the SiC phase at t = 3.2μs, thus making the interface bear a higher tension stress. As the two cracks develop further, their paths begin to deflect along the original interfaces at t = 3.6μs, accompanied by the interface debonding phenomenon. At t = 4.0μs, the degree of interface debonding further increases until the two cracks are completely connected to each other. It can be seen that, although brittle fracture of the SiC ceramic phase plays a key role in crack initiation, the existence of complex 3-D SiC/Al interfaces usually causes the generated cracks to be deflected before connecting with each other. This significantly retards the propagation of the cracks and thus increases the ductility of the composite materials.
Fig.17. The process from crack initiation and propagation to “interface debonding” in region A from.
In the final stage of failure (4.0-5.0μs), as shown in Fig. 18, there is an extensive region of collapse in the SiC phase, but the Al phase still retains a certain structural integrity. Fig. 19 shows the effective plain strain contours of the Al phase at different times. To observe the plastic deformation of the Al phase in 3-D space, the SiC phase is hidden. As shown in Fig. 19(a), there exists clear plastic deformation in the local, relatively narrow, regions in the Al phase at t = 4.0μs. At t = 5.0μs (see Fig. 19(b)), local necking and tearing fractures tend to be localized in those severely deformed regions.
Fig.19. The failure contours of the 3-D FE model at t=5.0μs and the effective plain strain contours of Al at different times.

Simulation of damage and failure processes of interpenetrating SiC/Al composites subjected to dynamic compressive loading
Acta Materialia 78 (2014) 190–202
文献2(2014):Experimental observation and numerical simulation of SiC3D /Al interpenetrating phase composite material subjected to a three-point bending load(SiC3D / Al双连通复合材料三点弯曲载荷的实验观察与数值模拟)
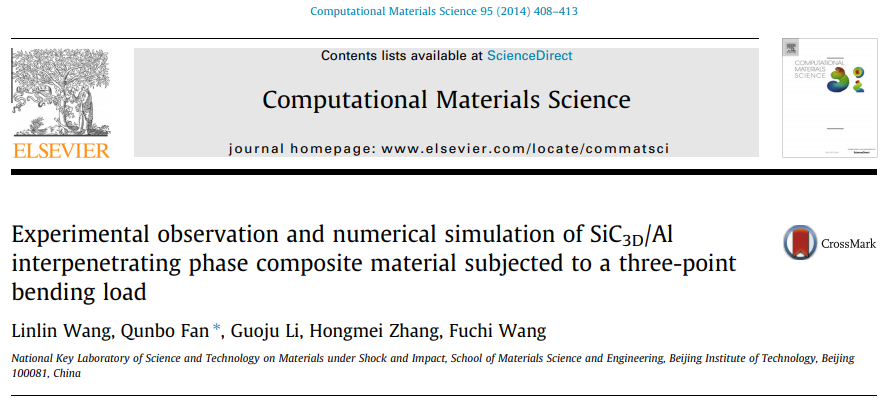
Both the experimental and simulation results indicated that crack propagation occurred predominantly in the SiC phase, which is consistent with the general understanding that crack propagation occurs in the brittle ceramic phase. The experimental test and the simulation were consistent at the macroscopic scale, with both methods indicating that the primary crack was roughly parallel to the loading direction.
Fig.6. Simulated crack growth path and micrograph showing primary crack in SiC3D /Al composite.
Subsequently, the generated microcracks propagated and amalgamated at t= 23.65 s to form a primary crack. The primary crack then propagated rapidly until the specimen ruptured. It was noted that the crack was finally terminated at a SiC–Al interface due to the greater plasticity of the Al phase that enabled it to deform at that point without cracking. Fig. 10(b) shows the stress contours of the SiC3D/Al composite at t= 22.9 s, where it is seen that a new stress concentration developed within the SiC above the Al phase, such that the primary crack bridged over the Al phase, then continued to propagate within the SiC ceramic material. Fig. 10(d) and (e) are micrographs of the crack growth path in SiC3D/Al composite after the experimental test. It is clearly seen that, before the primary crack was arrested, it propagated along the SiC–Al interface for some distance before bridging over the Al phase, in close agreement with the numerical simulation..
Fig.10. Crack propagation in SiC3D/Al composite: (a) simulated formation of primary crack; (b) stress contours of the SiC3D/Al composite at t= 22.9 s from simulation; (c) simulated examples of cracking behavior along the SiC–Al interface; (d) micrograph showing crack growth path during test; (e) micrograph showing crack bridging over the Al phase.

Experimental observation and numerical simulation of SiC3D /Al interpenetrating phase composite material subjected to a three-point bending load
Computational Materials Science 95 (2014) 408–413

京公网安备 11010802033099号
京ICP备2020038205号-1