通常将较高速度弹体碰撞靶板的力学过程称为侵彻,可以分为弹体侵入靶板、在靶板介质中运动和弹体穿出靶板等几个主要阶段。同其它学科的研究一样,试验、理论分析和数值模拟是侵彻问题研究的三类基本方法。当前在新型装甲结构的研究过程中,实验方法是最直接的方法,但是,实验研究为这一复杂过程提供的信息受到实验条件和测试技术的限制,无法充分体现和记录弹靶作用过程的瞬间现象。数值模拟方法可以对弹靶作用过程进行全物理、全过程模拟,获得不同时刻的物理图像和各种瞬变现象,并且其成本低,周期短,精确度有保证,可以大大提高研究的效率。因此,数值模拟在弹靶作用过程的研究中作用日益凸显。然而,在新型装甲结构的设计研究过程中,橡胶、陶瓷等多种新型装甲材料得以应用,装甲结构也较以往更为复杂,这些因素都为弹靶作用过程的数值模拟增加了难度,带来了新的挑战。
首页 >> 学术研究 >> 弹靶作用过程仿真
弹靶作用过程仿真
文献1(2020):Effect of the Layer Sequence on the Ballistic Performance and Failure Mechanism of Ti6Al4V/CP-Ti Laminated Composite Armor(层序对Ti6Al4V / CP-Ti叠层复合装甲抗弹性能及失效机理的影响)
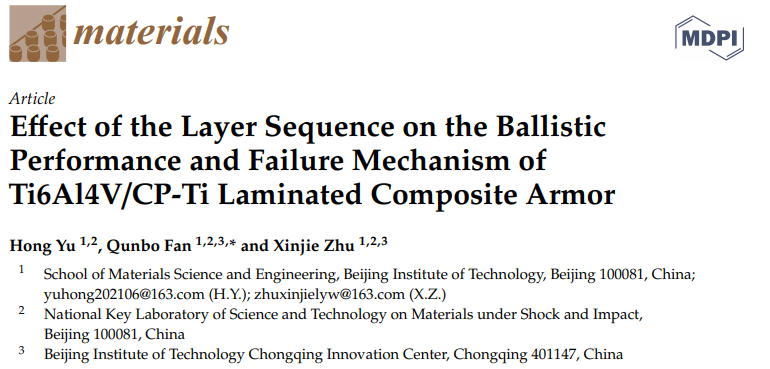
Figure 5 shows the strain distribution of the projec hye me do with het and lead jacket developed and plate during the penetration process. At t=35 μs, the steel core penetrated the target plate, and serious plastic deformation and failed quickly when interacting with the target plate. Severe plastic deformation with the effective strain of 0.3 occurred in the titanium alloy near the tip of the steel core in both schemes. For CPTi Ti64, the plastic deformation of the CP-Ti layer was also considerable At t=70 μs, the brass jacket and lead jacket penetrated the target plate, thus enlarging the crater on the front of the target plate of both T164/ CPTi and CPTi/Ti64, but almost half of the brass and lead had failed due to severe deformation. At t= 120 μs, the projectile had been stopped. The brass jacket and lead jacket were totally ripped off and most of them failed, causing a larger deformation on the target er, the tip of the steel core experienced small plastic deformations during penetration. Although Ti6A14V produces large plastic deformation in both schemes, the plastic deformation of CP-Ti in Ti64 CPTi is relatively small compared with CPTi/ T164.
Figure 5. The strain distribution of the projectile and plate during the penetration process: (a) Ti64/CPTi and (b) CPTi/Ti64.
Figure 6 shows the experimental and simulated macro morphologies of the cross-section along the penetration channel of the Ti6A14V/CP-Ti laminated plates. The damage to the rear face of the target plate is shown in the lower left inset. As is shown in Figure 6a, lamellar tearing occurred in the Ti6A14V that was indirectly connected to the penetration channel, and the rear face of the Ti64/CPTi plate underwent bulging without fracturing. Similarly, the numerical simulation results of the Ti64, CPTi plate(Figure 6b)revealed that bulging of the CP-Ti layer occurred without the deletion of elements The lamellar tearing generated in the CPTi/Ti64 plate was less extensive and narrower than that observed for the Ti64/CPTi plate(see Figure 6c). However, severe cracks were generated on the back of the target plate. As revealed by the numerical simulation results of the CPTi Ti64 plate(Figure 6d), element deletion occurred on the rear face of the target plate, that is, cracks were generated. Therefore the macro morphology shown by simulations closely corresponded to the experimental results.
Figure 6. Macro morphologies of the cross-section along the penetration channel of the Ti6Al4V/CP-Ti laminated composite armor: (a,c) Experimental results and (b,d) simulation results of the Ti64/CPTi plate and CPTi/Ti64 plate, respectively.

Effect of the Layer Sequence on the Ballistic Performance and Failure Mechanism of Ti6Al4V/CP-Ti Laminated Composite Armor
Materials 2020, 13(17), 3886
文献2(2020):Study of high-speed-impact-induced conoidal fracture of Ti alloy layer in composite armor plate composed of Ti- and Al-alloy layers(钛铝合金复合装甲板中钛合金层高速冲击诱导锥状断裂的研究)
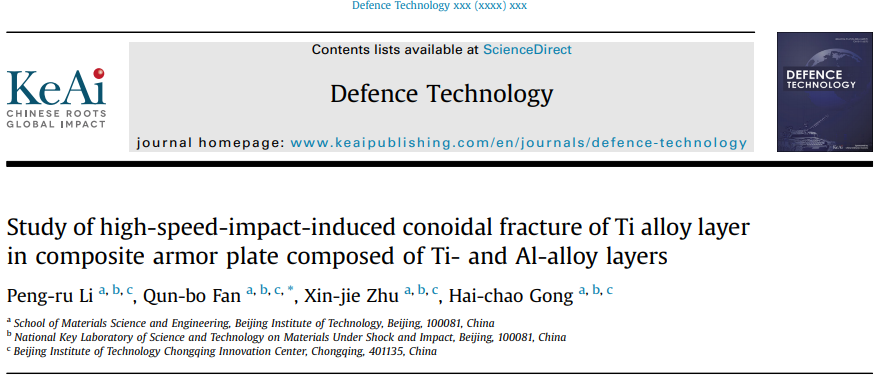
Crack propagation are shown in Fig. 10. In zone I, the distance between the tip of the main cracks and the target surface was approximately 4 mm, with sub-cracks growing perpendicular to the main crack. The plate underwent substantial plastic deformation upon penetration by the projectile, and the stress triaxiality in the shear region was between -2.0 and -1.0. From Fig. 4, it can be seen that the target materialwas in the shear fracture mode. During the penetration process, the shear stress dominate regions gradually decrease, at the same time gather below the projectile. In contrast, the red part, i.e., the area with triaxiality greater than 0, increased significantly from 18 μs; from 18 μs to 100 μs, the triaxiality in this zone was between 0 and 0.5 in this period, corresponding to the mixed mode of shear and ductile fracture. Further, from 22 μs to 40 μs, in zone III, cracks initiated and expanded gradually; the triaxiality was relatively large, i.e., between 1.0 and 1.9, indicating that the ductile fracture mode was dominant. Notably, the period in which cracks exist in zone III is dependent on the other two zones, and this period is within the period in which zone II exists.
Fig.10. Time-history analysis of stress triaxiality and timeline of crack propagation.
Because the adiabatic shear band was closely related to the loading condition, the numerical simulation method was used for the in-depth study of the target stress state. The shear stress nephogram and the maximum principal stress nephogram are shown in Fig. 12. From 4 μs to 6 μs, the shear stress remained concentrated in zone I, and the red and blue areas in the figure reflected the shear stress in the opposite directions. From Fig. 12 (a) and (c), we can see that the maximum value was about 0.9 GPa. Moreover, compared with the shear stress, the principal stress in this area was relatively dispersed, with the maximum value of about 0.2 GPa (Fig. 12(b) and (d)). Furthermore, the formation of cracks in zone I was mainly due to the shear stress.
Fig.12. Shear stress nephogram and the maximum principal stress nephogram of zone I: (a) shear stress nephogram at 4 ms; (b) maximum principal stress nephogram at 4 ms; (c) shear stress nephogram at 6 ms; and (d) maximum principal stress nephogram at 6 ms.

Study of high-speed-impact-induced conoidal fracture of Ti alloy layer in composite armor plate composed of Ti- and Al-alloy layers
Defence Technology, 2020.
文献3(2020):圆筒型陶瓷钛合金芳纶三单元层复合靶板结构抗弹性能数值模拟及其内在机理(Ballistic performance simulation of cylindrical ceramic Titanium/ Aramid Three-Layered Composite Targets and the Underlying mechanism)
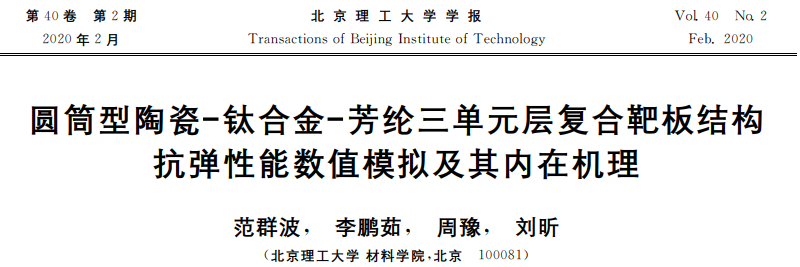
弹体采用53式7.62mm口径穿甲燃烧弹,弹芯由T12A合金钢加工而成,头部为尖卵形,直径6mm,长度27.5mm.弹芯的几何模型如图1所示。仿真过程中弹头的变形行为与其本构模型密切相关,通过失效判据删除单元体现磨蚀现象。复合靶板形状为圆筒状,为节省运算时间,采用1/2有限元模型,如图2所示。复合靶板高为93mm,内径为258mm,从内到外各单元层依次为芳纶纤维板、Ti- 6A1-4V合金板与Al2O3陶瓷板,厚度分别为3,6与6mm.陶瓷单元层由弧形陶瓷块拼接而成,陶瓷块的高为31mm,对应的圆心角为12°。弹体以760m/s的速度着靶,使用非线性动力学有限元软件 LS-DYNA模拟弹靶作用过程。
图1 7.62mm口径穿甲燃烧弹弹芯及圆筒型复合靶板结构有限元模型
图3展示了靶试试验与数值模拟结果中复合板损伤形貌对比图,试验与仿真中弹体初始速度大小均为760m/s.根据图3可以看出,陶瓷块开裂破碎,弹体最终撞击在钛合金单元层上形成凹坑,模拟结果与靶试试验结果现象一致。此外,数值模拟中复合靶板穿深为9.3mm,试验测得的复合靶板穿深为8.5mm,相对误差为94%。误差相对较小,表明了模拟计算的可靠性。误差出现的原因可能为模拟计算中采用理想化各项同性材料模型与实际情况略有差异。
图3 靶试实验与数值模拟钛合金板损伤形貌对比图
文献4(2017):SiC/Al 双连通复合装甲材料抗侵彻性能宏–微观跨尺度模拟(Multi-scale Simulation of Interpenetrating SiC/Al Composite Armor Materials Subjected to Impact Loading Using a Macro-micro Approach)
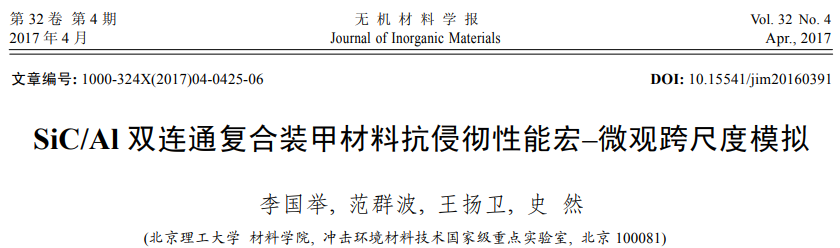
首先,利用LS-Dyna软件在靶板宏观结构模型中选定待研究微区,进行弹靶作用过程模拟并输出该微区载荷信息;将载荷施加于SiC/Al 双连通复合材料微观组织三维模型轮廓上,模拟其动态响应过程,最终实现宏观靶试–复合材料微观组织的跨尺度有限元模拟。从靶板抗侵彻过程中损伤云图中,可以看出SiC/Al 材料损伤位置主要分布在弹着点位置正下方(微区Ⅰ)和与弹道方呈45°角的锥形区域(微区Ⅱ)。
图6 跨尺度有限元模拟示意图和SiC/Al双连通复合装甲材料抗侵彻损伤云图
主裂纹形成过程:当t=4.0 μs 时,裂纹继续在界面处扩展并开始向陶瓷内部扩展,扩展方向大致与轴向平行;当t=6.0 μs 时,离散分布的裂纹之间开始产生桥连;t=6.5 μs 时,形成了贯穿整个模型的两个轴向主裂纹。随后,在主裂纹部分产生更多的分支裂纹,在t=8.5 μs 时最终交织成网状;裂纹萌生过程:在t=4.5 μs 时,界面靠近陶瓷相一侧开始产生裂纹,随后, 裂纹绕界面扩展并在陶瓷相内部产生新的垂直于轴向的水平裂纹,当t=7.0 μs 时模型内部产生多处离散分布的界面裂纹和陶瓷相内部的水平裂纹; 锥形主裂纹形成过程:当t=7.5 μs 时,在陶瓷相内部产生更多的离散分布的水平裂纹;当t=8.0~9.0 μs 时,界面裂纹开始向陶瓷相内部扩展并与水平裂纹搭接,扩展方向与轴向夹角呈45°,两界面处的裂纹开始桥连,桥连方向为45°方向,当t 达到11.0 μs 时形成两条锥形主裂纹。
图11 轴向主裂纹的形成过程和裂纹绕界面的扩展过程和锥状裂纹的形成过程
文献5(2017):Study on Protection Mechanism of 30CrMnMo-UHMWPE Composite Armor(30CrMnMo-UHMWPE复合装甲防护机理研究)
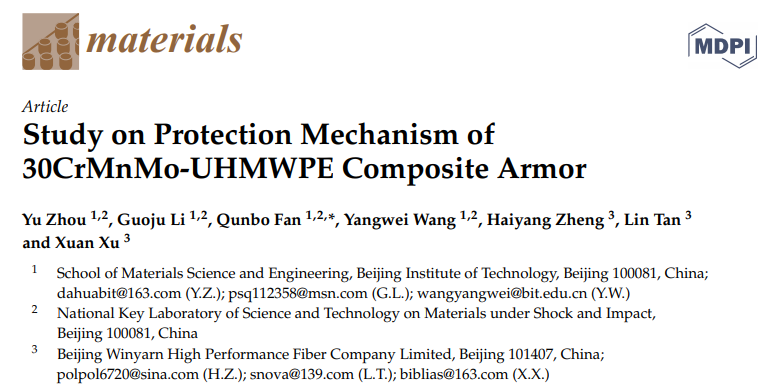
Figure 3 shows the finite element simulation results of the fragment penetrating the composite armor at various times. The initial state at 0μs, and the steel and PE laminates penetrated at 18μs and 60μs are shown in Figure 3a–c, respectively. At 150μs, the fragment becomes stuck in the witness plate (see Figure 3d).
Figure.3. Simulation results showing penetration at different times (a) 0μs (b) 18μs (c) 60μs (d) 150μs.
The back morphology of the PE laminate after the ballistic test is compared with the FEM-simulated morphology (see Figure 4). Consistent with the test result, the simulation result (Figure 4a) indicates that several back layers of the laminate coalesce to form a large back bulge during fragment penetration (Figure 4b).
Figure.4. Backfaces of the PE laminate after the (a) FEM simulation; and (b) ballistic test.

Study on Protection Mechanism of 30CrMnMo-UHMWPE Composite Armor
Materials 2017 10(4):405-

京公网安备 11010802033099号
京ICP备2020038205号-1