完成形变加工与热处理之后,钛合金得以取得满足使用需要的性能并进入实际的应用服役阶段。一般来说,钛合金在各领域服役中发生的塑性变形行为可以分为准静态塑性变形与动态塑性变形。其中,准静态(一般指应变率不高于10-3/s数量级)塑性变形行为在钛合金的服役过程中十分常见(如用于支架、人造骨及各类结构件等用途时),近几十年来伴随钛合金的应用越来越普及受到了广泛关注。钛合金在准静态下的塑性变形模式包括传统的位错滑移与孪晶,在双相钛合金中又以位错滑移为主导因素。其中,大多数钛合金中α与β两相同时存在,在变形过程中必然相互影响。有必要在考虑两相共存的条件下,对α相、β相各自的变形模式,两相内部与两相之间的滑移传递规律等进行研究。近年来,针对变形过程中两相的相互影响逐渐受到关注。得益于前期工作,人们对钛合金变形中两相相互作用下的滑移系启动与滑移传递规律已经有了一定的认识。
首页 >> 学术研究 >> 钛合金微观组织准静态力学响应行为
钛合金微观组织准静态力学响应行为
文献1(2020): Microstructure evolution and mechanical properties of a hot-rolled Ti alloy(轧制态钛合金微观组织演化及力学性能)
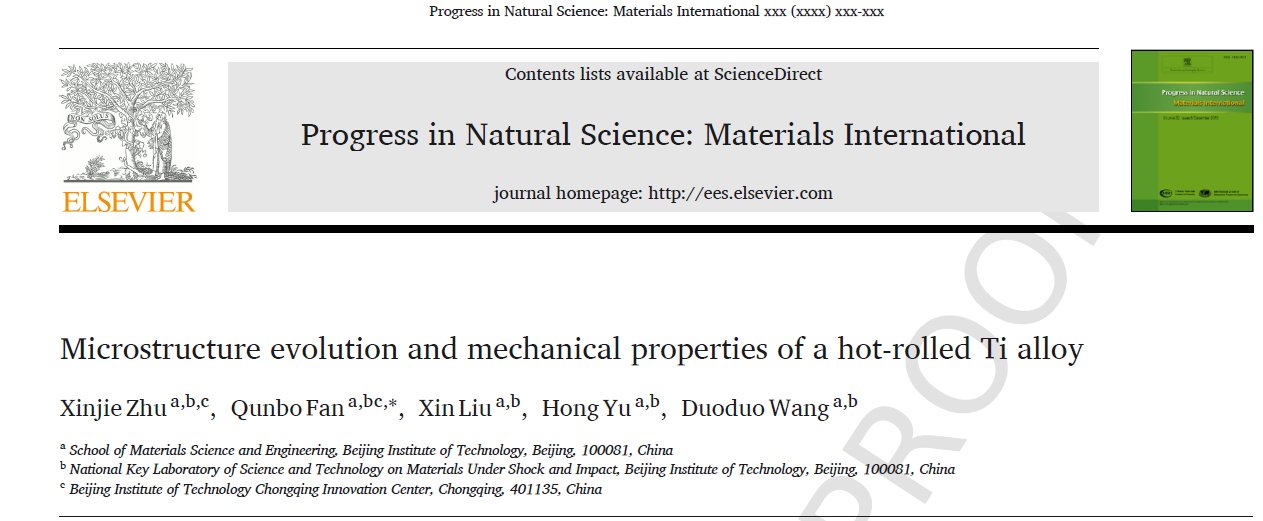
Based on the statistical data derived from Fig. 4(a), the misorientation angle distribution of grain boundaries in the central region can be obtained and is displayed in Fig. 4(g). The fraction of HAGBs in β phase is 23.4%. Moreover, the fraction of HAGBs in α phase is 27.2% and the transition from LAGBs to HAGBs is continuous. This indicates that dynamic recovery occurs mainly in β phase. In addition, relatively slight DRX also occurs in α phase. The misorientation angle distribution of grain boundaries in the position of S = 0.4 is obtained and displayed in Fig. 4(h) based on the statistically derived data from Fig. 4(b). The fraction of HAGBs in β phase is 8.4%, illustrating the occurrence of more intense dynamic recovery in β phase compared with that in the region of S = 0. Moreover, the fraction of HAGBs in α phase is 40% and the transition from LAGBs to HAGBs is continuous, indicating the occurrence of more intense DRX in α phase compared with that in the region of S = 0. The misorientation angle distribution of grain boundaries in the position of S = 0.8 is displayed in Fig. 4(i) based on the statistical data derived from Fig. 4(c). The fraction of HAGBs in β phase is 3.9%, illustrating the occurrence of extremely intense dynamic recovery in β phase. Moreover, the fraction of HAGBs in α phase is 49.9% and the transition from LAGBs to HAGBs is continuous. This indicates the occurrence of the most intense DRX in α phase compared with that in regions of S = 0 and S = 0.4. In contrast, the level of DRX in β phase in the region of S = 0.8 is the lowest among these specimens.
Fig. 4. EBSD grain boundary maps, grain boundaries in inverse pole figures and corresponding misorientation distribution maps of the hot-rolled titanium alloy sheet: (a), (d), (g) S = 0; (b), (e), (h) S = 0.4; (c), (f), (i) S = 0.8.
The microstructural orientation maps of α and β phases in the specimens observed from the TD are shown in Fig. 5(a)-(f). The α and β phases gradually concentrate on some orientations with the increase of distance from the central region, such as the {0001} for the α phase and {001} for the β phase.The pole figures of α and β phases in these specimens are shown in Fig. 5(g) and (h), respectively. For α phase, the strongest texture locates in the {0001} pole figure compared to that in the {01–10} pole figure and the {-12-10} pole figure, as shown in Fig. 5(g). In the central region (S = 0), the strength of the {0001}α texture is 6.99. With the increase of distance from the central region, the strength of the {0001}α texture increases to 11.29 (S = 0.4) and 20.70 (S = 0.8).
Fig. 5. Orientation maps of specimens: (a) α phase and (b) β phase of S = 0; (c) α phase and (d) β phase of S = 0.4; (e) α phase and (f) β phase of S = 0.8; (g) and (h) pole figures of α phase and β phase in the hot-rolled titanium.
In the last stage of the hot rolling process, a great number of elongated grains in all regions are fragmented into finer grains, especially in the central region. Moreover, the grain fragmentation disturbs the preferred orientation arrangement of grains concurrently, making the texture strength of α and β phases in the central region lower than that near the surface. At the same time, friction stress near the surface may weaken the strength of some textures [28], such as the {101}β texture. In addition, the level of the total DRX is higher than that near the surface due to their more driving force of the total DRX in the central region. What should be noticed emphatically here is that the DRX in α phase exhibits an increasing trend with the increase of distance from the central region, which is not consistent with the theoretical prediction and contrary to that of the β phase, as shown in Fig. 8(d). This phenomenon is attributed to the allocation of energy consisting of the accumulated deformation energy and thermal energy during the hot rolling process. With the increase of the distance from the center region, the deformation energy descends down and the local temperature becomes lower and lower gradually. Thus, the α→β phase transformation is inhibited, making the fraction of α phase increase correspondingly. Simultaneously, the driving force of DRX in α phase increases, strengthening the DRX in α phase in the regions near the surface. Therefore, the fraction of α phase and DRX in α phase exhibit an increasing trend with the increase of the distance from the central region. Furthermore, with the increase of distance from the central region, the driving force of DRX in β phase decreases. Thus, the fraction of β phase and DRX in β phase exhibit a decreasing trend.
Figure 8. Schematic of microstructural evolution along the thickness direction. (a) Original microstructure of titanium alloy. (b) Hot-rolled microstructure showing different deformation for the central region and the surface where dislocations appear. (c) DRX grains appear in the central region. (d) Microstructure after hot rolling process showing different grain size and the level of DRX for the central region and the surface.

Microstructure evolution and mechanical properties of a hot-rolled Ti alloy
Progress in Natural Science: Materials International xxx (xxxx) xxx-xxx
文献2(2020):Effect of tungsten micro-scale dispersed particles on the microstructure and mechanical properties of Ti-6Al-4V alloy(钨微尺度分散颗粒对Ti-6Al-4V合金组织和力学性能的影响)
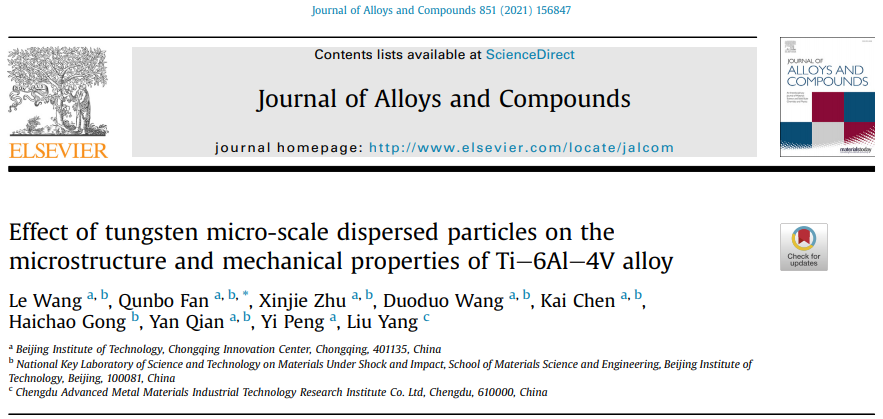
The starting materials for mechanical milling were Ti-6Al-4V powders with less than 150 μm in particle size (as shown in Fig. 1(a)) and W powders with ~5 μm in particle size (as shown in Fig. 1(b)). The chemical composition of the Ti-6Al-4V powders was shown in Table 1. The two kinds of powders were mechanically mixed at 250 rpm for 10 h using a SPEX 8000D high energy shaker ball mill (SPEX 8000 mill/mixer, Nanjing University col., Ltd) to avoid the agglomeration ofWpowders and obtain a homogeneous composition during the sintering process. Stainless steel balls with a diameter of 6 mmwere used to mix the powders and the ball-tocharge ratio was 10:1. As a comparison, pure Ti-6Al-4V powders were also prepared for reference under the same conditions. The milled TC4 powders and TC4/W mixed powders were shown in Fig. 1(c) and (d).
Fig. 1. The surface morphology of powders. (a) origin TC4 powders, (b) originWpowders, (c) ball-milled TC4 powders, and (d) ball-milled TC4/W mixed powders. (e) enlarge of (d).
Fig. 7 exhibits the fracture surfaces of TC4 and TC4-5%W alloys. As shown in Fig. 7(a), it was found that the fracture surface of TC4 alloy mainly had a brittle cleavage fracture mode. The river patterns were present in the fracture surface of TC4, which contained numerous shallow and parallel tearing ridges. Moreover, A regions (marked by red rectangular area) and B regions (marked by yellow rectangular areas) showed the typical intergranular fracture characteristics, which should be caused by the fracture of the continuous αGB layers. Similar results have been reported by Berg et al. and Cao et al. Besides, therewere still some dimples in the fracture surface of TC4 alloy, but the number of these dimples was very small and most of them were shallow, leading to a decrease of ductility. On the contrary, Fig. 6(b) shows that the fracture surface of TC4-5%W alloy has a ductile fracture mode, which reveals a large number of dimples (marked by arrows). These dimples were deeper than that of TC4 alloy, which also demonstrated that TC4-5% W alloy possessed higher ductility, compared with TC4 alloy. Meanwhile, it can be found that W particles (marked by black arrows in Fig. 6(b) and the pink rectangular frame in Fig. 7(c)) were pulled out of the tensile sample after the tensile test. The region marked by the rectangular frame in Fig. 7(c) was detected by EDS, which suggested that the particle pulled out from the TC4 matrix is W particle. These W particles can effectively inhibit dislocation movement during the tensile process, thus increasing the strength of TC4-5%W alloy.
Fig. 7. Fracture surfaces of (a) TC4 and (b) TC4-5%W. The EDS regions of TC4-5%W alloy (c) and the EDS mapping images of W particle and TC4 matrix (d).

Effect of tungsten micro-scale dispersed particles on the microstructure and mechanical properties of Tie6Ale4V alloy
Journal of Alloys and Compounds 851 (2021) 156847
文献3(2020):Effect of He content on microstructure, mechanical properties and He thermal desorption behavior of W film fabricated by RF magnetron sputtering(氦含量对射频磁控溅射制备的钨薄膜组织、力学性能和热解吸行为的影响)
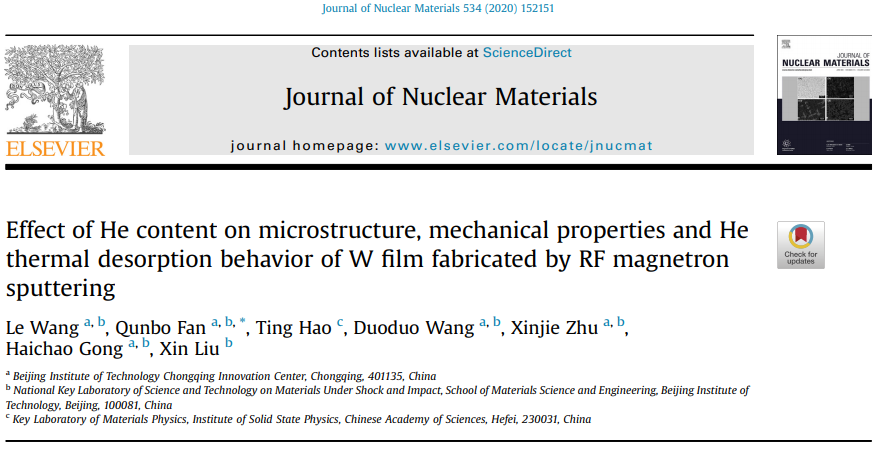
Fig. 1 shows the effect of He atoms on the surface morphology of W films. As shown in Fig. 1, the structure of both pure W films and He-charged W films are very compacted. For W film deposited by magnetron sputtering, there may be some nano-scale grains in films, which can be hardly detected by SEM. Moreover, not all grain boundaries in the deposited film can be easily shown in SEM images, which may cause some the measurement errors. Therefore, the SEM images can’t assess accurately the average grain size. Nevertheless, the SEM images of surface morphology still can indicate roughly that the grain size becomes smaller with increasing He/Ar ratio. The trend of the change of grain size obtained from the surface SEM images corresponds to the following result of grain size calculated by the XRD peak profile analysis.
Fig. 1. The surface SEM images of W films deposited on the Si substrate at RT under the different He/Ar ratios: (a) 0; (b) 1; (c) 2; (d) 3.
Fig. 6(a-c) shows the distribution of He bubbles in W films fabricated at different He/Ar ratios, and the mean diameter of these bubbles was estimated to be about 1.0 nm. As Fig. 6(a) shown, a large number of He bubbles distributed in the grain interiors and around the grain boundaries (GBs) ofWfilms. In particular, the size of He bubbles trapped by GBs was bigger than that located in grain interiors. Moreover, these He bubbles around GBs were accumulated and connected to each other to form a necklace-like line as shown in Fig. 6(a). The above results indicate that the nucleation and growth of He bubbles are preferential on the GBs for rapid diffusion than that in the grain interiors, which had been found by J.H. Evans et al. and O. El-Atwani et al. This is because a large number of vacancies exist on the GBs so that more He atoms can be trapped by vacancies to form bubbles at GBs. Meanwhile, it was easily found that the shape of He bubbles in grain interiors was spherical and the shape of He bubbles trapped by the GBs was ellipsoidal. For this difference of He bubble shape, a similar phenomenon had been studied by A. Ofan et al. In their work, they believed that the shape of He bubbles is closely related to the surface free energy and the elastic free energy. As a result, in our experiments, when the surface energy was dominated, the spherical He bubbles in grain interiors were formed. When the elastic energy played amajor role in this process, elongated He bubbles along the grain boundary were formed. For W films prepared at He/Ar=2 and He/Ar=3, He bubble size becomes a little larger than before, but the mean diameter of these bubbles was estimated to be still less than 2 nm, as shown in Fig. 6(b) and (c).
Fig. 6. TEM images of W films fabricated at different He/Ar ratios: (a) He/Ar = 1; (b) He/Ar = 2; (c) He/Ar = 3.

Effect of He content on microstructure, mechanical properties and He thermal desorption behavior of W film fabricated by RF magnetron sputtering
Journal of Nuclear Materials 534 (2020) 152151
文献4(2020):Study of high-speed-impact-induced conoidal fracture of Ti alloy layer in composite armor plate composed of Ti- and Al-alloy layers(钛铝合金复合装甲板中钛合金层高速冲击诱导锥状断裂的研究)
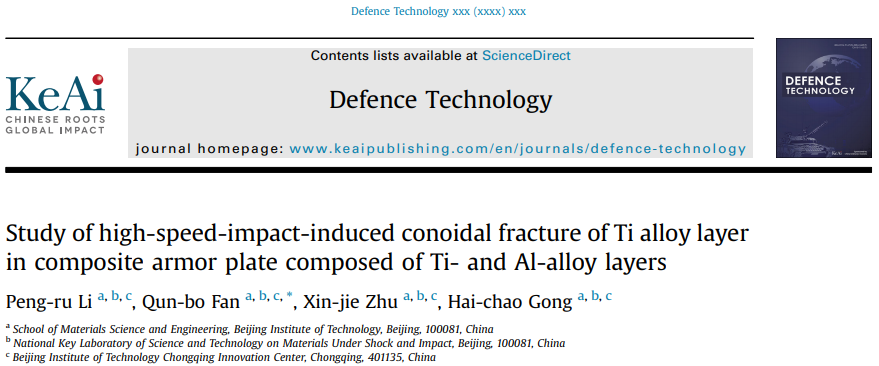
In Fig. 11(a), a scanning electron microscopy (SEM) image of zone I is shown, and the morphological features of the scanning area are shown in Fig. 11(b). The surface of the crack in the area enclosed by red lines was rough and showed connected voids. Further, another crack in the area enclosed by the blue lines had a smooth surface and sharp tip, indicating that the shear crack propagates as a result of shear deformation. Moreover, SEM observation revealed that most of the cracks were accompanied by adiabatic shear bands, thus indicating the main cause of the cracks. Under the condition of loading at a high strain rate, the temperature rise of the shear band was extremely high. Because of the extremely uneven deformation in the band, many hot spots with abnormal temperature existed. At some hot spots, microvoid nucleation occurred under tensile or shear stress. As is shown in Fig. 11(c), upon projectile impact under a high-strain-rate loading,voids nucleated at the interface between the a phase and b phase in the titanium alloy target plate.
Fig.11. Microscale morphologies in zone I: (a) SEM scanning area in zone I; (b)microscale morphology at 200 × magnification; and (c) microscale morphology at 500 × magnification.
The microstructural characteristics in zone II are shown in Fig. 14. The area enclosed by white lines in Fig. 14 (a) was observed by SEM, and the morphological features of the area are shown in Fig. 14 (b). A microcrack with a smooth surface and sharp tip was located at the interface between the adiabatic shear band and the matrix. Under the applied stress, the deformation of the matrix part and the shear band was not synchronous, forming an elongated microcrack. In the shear band, discontinuous voids connected to the microcrack are visible. Fig. 14 (c) shows the voids in the matrix, mainly in the sharp interface area between the α phase and β phase.
Fig. 14. Microscale morphologies in zone II: (a) SEM scanning area in zone II; (b) microscale morphology at 200 × magnification; and (c) microscale morphology at 1500 × magnification.

Study of high-speed-impact-induced conoidal fracture of Ti alloy layer in composite armor plate composed of Ti- and Al-alloy layers
Defence Technology, 2020.
文献5(2020): Plastic deformation mode and α/β slip transfer of Tie5Al-2.5Cr-0.5Fe-4.5Mo-1Sn-2Zr-3Zn titanium alloy at room temperature(Tie5Al-2.5Cr-0.5Fe-4.5Mo-1Sn-2Zr-3Zn钛合金室温塑性变形形式和α/β滑移)
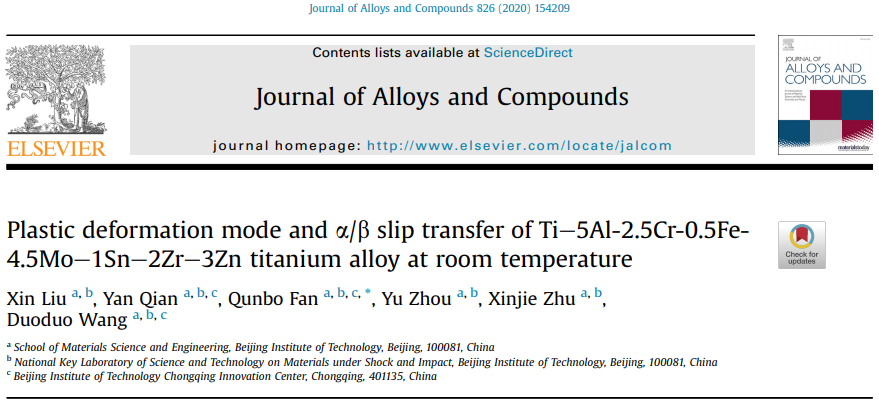
In the early stage of tensile deformation (Fig. 5a), the post-deformation morphology differed only slightly from the pre-deformation morphology. However, the crystal orientation changed with sub-grain boundary migration and substructure formation. The density of sub-grain boundaries increased significantly as the deformation progressed (Fig. 5b). In the later stage of deformation (Fig. 5c and d), the microstructure changed considerably (compared with the microstructure in the early stage), owing to the generation and migration of new grain boundaries and sub-grain boundaries.
Fig.5. OIM of the observed region with different strain.
Several features of slip activity and slip transfer could be summarized as follows: (1) Compared with other slip systems, prismatic slip systems could be activated (e.g., by the slip transfer) with a lower Schmid factor. (2) The crystal orientation changed during deformation, and adjacent grains under coalescence or splitting adapted to the overall deformation. (3) Slip transfer was partially blocked due to a large misorientation angle, and occurred with a very large misorientation angle resulting from high Schmid factors for the incoming or outgoing slip.
Fig.11. Slip activation and slip transfer in a specific region: (a) 4% strain, morphology and phase distribution, (b) 4% strain, Euler angle distribution, (c) 7.8% strain, morphology and phase distribution, (d) 7.8% strain, Euler angle distribution.

Plastic deformation mode and α/β slip transfer of Tie5Al-2.5Cr-0.5Fe-4.5Mo-1Sn-2Zr-3Zn titanium alloy at room temperature
Journal of Alloys and Compounds 826 (2020) 154209
文献6(2020):In-situ investigation via high energy X-ray diffraction of stress-induced (0002)α→(110)β transformation in a Ti-5.5Mo-7.2Al-4.5Zr-2.6Sn-2.1Cr alloy(利用高能X射线衍射对Ti-5.5Mo-7.2Al-4.5Zr-2.6Sn-2.1Cr合金中应力诱导(0002)α→(110)β相变进行原位研究)
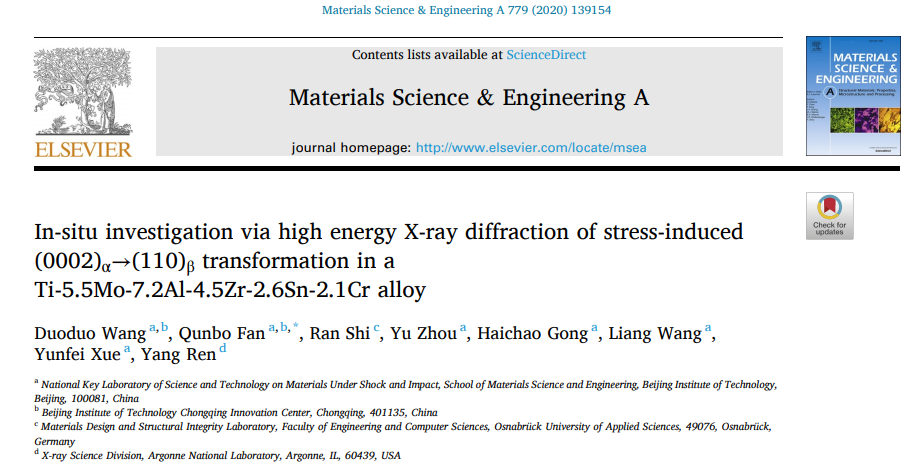
The equilibrium phase diagram of the Ti-5. 5Mo-7. 2A1-4.5Zr-26Sn-2.1Cr titanium alloy is constructed using JMatPro software, as illustrated in Fig. 2(a). The amount of β-Ti will increase monotonically with increasing temperature, whereas α-Ti disappears completely at a temperature of ~895℃. Therefore, the β-transus temperature (Tβ)is ~895℃. The initial scanning electron microscopy of the alloy in Fig. 2(b)reveals the bi-modal microstructure which consists of equiaxial primary α phase with a mean diameter of -3 μm and precipitated secondary α lamellae (length:~3-4μm)in β matrix. Furthermore, the microstructure is accurately reproduced at the center of the dog-bone-shaped specimen via EBSD. Fig. 2(c) shows the 400 x 400μm2 phase distribution map, collected at a step size of 0.5μm. The volume fractions of the hexagonal-close-packed α phase (red) and the body-centered-cubic β phase (blue) are 44% and 56%, respectively.
Fig.2. Equilibrium phase diagram and initial microstructure of the heat-treated Ti-5.5Mo-7.2Al-4.5Zr-2.6Sn-2.1Cr titanium alloy: (a) equilibrium phase diagram, constructed using JMatPro software, (b) scanning electron microscopy morphology, (c) phase distribution map obtained via EBSD.
Fig. 11(a) shows a TEM-BF micrograph of the specimen subjected to 3% strain. In the early stage, irreversible plastic deformation is retained in the form of dislocation lines at the grain boundaries (indicated by the arrows in Fig. 11(a)). As the strain increases further to 5% (Fig. 11(b)), the multiplication of dislocations leads to an increase in the accumulated dislocation density. Fig. 11(c) shows a high-magnification image of the region enclosed in the circle (see Fig. 11(b)). A mass of dislocations accumulates in local regions, thereby resulting in dislocation tangles, as indicated by the arrows in Fig. 11(c). Therefore, the interaction between dislocations is considerable, and acts as an obstacle to further dislocation motion. The strain hardening behavior at a strain of ~5% (Fig. 5 inset) confirms this hypothesis. A TEM-BF micrograph obtained at 8% strain (Fig. 11(d)) shows that dislocation tangles are quite prominent at this level of strain. Moreover, in the cellular dislocation structure (indicated by a red dashed box in Fig. 11(d)), low-density dislocation regions are surrounded by cell walls with a relatively high dislocation density. Fig. 11(e) shows a high-magnification image of the region enclosed in the circle (see Fig. 11(d)). The dislocation tangles are gradually released and cross-slipping occurs, as indicated by the arrows in Fig. 11(e). This results in dislocation annihilation between opposite-type dislocations. The softening behavior induced by this annihilation and the strain hardening behavior will reach a dynamic equilibrium, corresponding to the steady-state flow stage in Fig. 5. In addition, the lack of a special BOR and stress states between the (0002) and (110) reflections (see Fig. 10) may have prevented the stress-induced (0002)α)→(110)β)transformation during the plastic deformation stage.
Fig.11. TEM micrographs obtained at various strains: (a) BF image at 3% strain, (b) BF image at 5% strain, (c) dislocation tangles, magnified view of the region enclosed in the circle shown in (b), (d) BF image at 8% strain, (e) cross-slipping dislocation, magnified view of the region enclosed in the circle shown in (d).

In-situ investigation via high energy X-ray diffraction of stress-induced (0002)α→(110)β transformation in a Ti-5.5Mo-7.2Al-4.5Zr-2.6Sn-2.1Cr alloy
Materials Science & Engineering A 779 (2020) 139154
文献7(2018):Correlation between dislocation-density-based strain hardening and microstructural evolution in dual phase TC6 titanium alloy(双相TC6钛合金中基于位错密度的应变硬化与组织演化的关系)
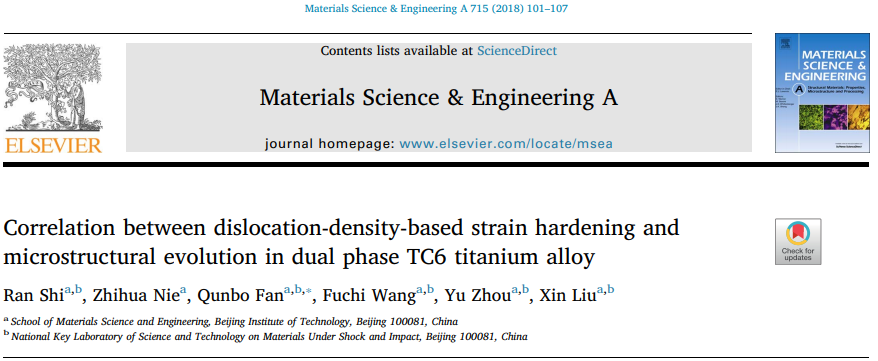
Fig.7 shows the dislocation microstructure at 1.5% strain. In this stage, irreversible plastic deformation is stored in the form of dislocation tangles (indicated by the arrows in Fig. 7(a)). Moreover, the strain-induced α-to-β phase transformation, described by the {11 2 0}α// {200}β orientation relation (see Fig. 7(b)), occurs at this strain level. Plane A in the figure corresponds to {11 2 0}α. From the reciprocal diffraction spot, values of 2.083 Å and 1.466 Å are calculated for the {110}β and {002}β planes, respectively. These values are both lower than the corresponding standard values (2.348 Å and 1.660 Å), indicating that the β phase is in the compressive state.
Fig.7. TEM bright-field micrographs of the sample subjected to 1.5% strain, (a) dislocation tangles, (b) strain-induced phase transformation from the α phase to the β phase.
With loading, interactions between dislocations increase leading to a mass of dislocation arrays and cells. The cell wall has high dislocation density, and the cell interior is a low-density dislocation region. An image of a typical dislocation microstructure at 2% strain is shown in Fig. 8(a). As the figure shows, the dislocations of slip systems associated with a particular direction in the α phase form numerous sub-grain boundaries. At 5% strain, slip systems associated with another direction are activated, and the sub-grain boundaries (formed by dislocations of the first direction) act as obstacles, as shown in nanopillar compression tests. The interaction between slip systems associated with different directions leads to curved dislocation lines and dislocation tangles (see Fig. 8(b)) and, in turn, strain hardening (see Fig. 5). When the strain increases to 7%, the dislocation tangles are broken and shear banding begins (as indicated by the engineering strain-stress curve in Fig. 1, after 7% strain, significant softening occurs and the stress decreases). Dislocations on planes A {11 2 0}α and B {1 21 0}α form a crisscrossing dislocation pattern, as shown in Fig. 8(c).
Fig.8. TEM bright-field micrographs of samples subjected to: (a) 2% strain, showing numerous sub-grain boundaries formed by dislocations, (b) 5% strain, showing curved and tangled dislocation lines, (c) 7% strain, showing a crisscrossing dislocation pattern.

Correlation between dislocation-density-based strain hardening and microstructural evolution in dual phase TC6 titanium alloy
Materials Science & Engineering A 715 (2018) 101–107
文献8(2017):Three-dimensional microstructure-based micromechanical modeling for TC6 titanium alloy(基于三维微观组织的TC6钛合金微观力学建模)
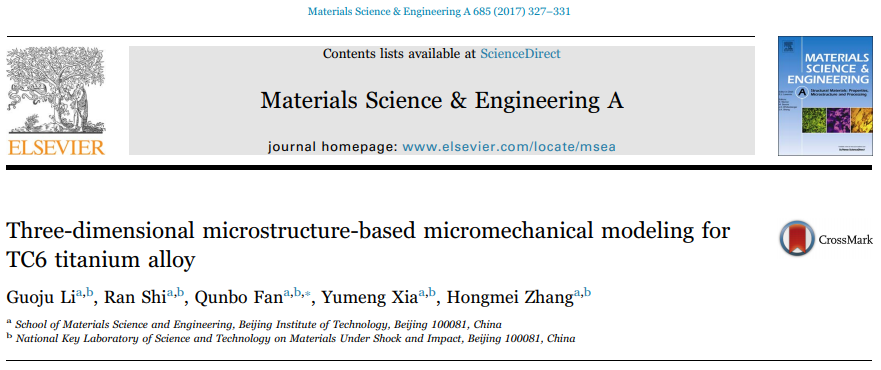
The commercial software Ansys/LS-Dyna was used to simulate the deformation process of nanoindentation of a 10×10×5 μm3 (length×width×height) workpiece. A Berkovich indenter was used; this indenter has a triangular-based pyramid, which was modeled as an isotropic, purely elastic solid with Poisson's ratio and Young's modulus of νi =0.07 and Ei =1100 GPa, respectively. In addition, FEM was used to fit the experimental load-displacement data obtained from the nanoindentation tests on the primary α phase in the TC6 titanium alloy. The constitutive parameters were varied in order to match the simulated curves with the experimental ones. After a parametric study consisting of 216 trials, we obtained a few bilinear constitutive law parameters (135 GPa, 880 MPa, 6.5 GPa). As the figure shows, the simulation of the 500-nm-load displacement curve, as well as the shape and size of the nanoindent are well-matched with the experimental results.
Fig.3. Determining the constitutive relations of the primary α phase: (a) 3D nanoindentation model setup and (b) comparison of numerical and experimental P-h curves as well as the shape and size of the nanoindent in the primary α phase of the TC6 titanium alloy.
Numerical simulations are performed by using an Ansys/LS-Dyna code to model the micromechanical response of TC6 titanium alloy subjected to uniaxial tensile loading at a constant strain rate of 1.0×10-5s-1. The simulated true stress-strain response concurs with the experimentally determined response, which illustrates the current model just considering isotropic bilinear constitutive law is acceptable. The entire elastic plastic deformation process can be divided into four stages, based on the stress concentration among the constituent phases in the alloy. These stages are the: (I) first stress concentration (εt≤0.007) in the primary α phase, (II) stress concentration in the secondary α phase (0.007 < εt ≤0.009), ( III) stress concentration in the β phase (0.009≤εt ≤0.010), and (IV) second stress concentration in the primary α phase (0.010 < εt ≤0.05).
Fig.4. Finite element analysis based on a 3D microstructure model of TC6 titanium alloy subjected to uniaxial tension loading: (a) 3D microstructure finite element model of the TC6 titanium alloy; (b) Numerical and experimental true stress-strain responses obtained under tensile loading, and effective stress contours at points A (εt =0.007), B (εt=0.0088), C (εt =0.010), and D(εt =0.050).

Three-dimensional microstructure-based micromechanical modeling for TC6 titanium alloy
Materials Science & Engineering A 685 (2017) 327–331
文献9(2016):Elastic plastic deformation of TC6 titanium alloy analyzed by in-situ synchrotron based X-ray diffraction and microstructure based finite element modeling(TC6钛合金的弹塑性变形的原位同步加速器X射线衍射分析和基于微观结构的有限元建模)
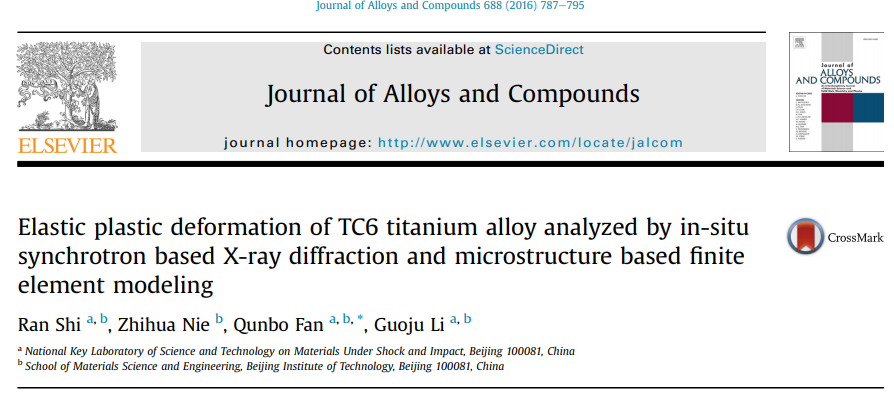
The plastic strain and Von Mises effective stress contours at A, B and C are shown in picture. Point A (εT =0.005) was chosen to be in the elastic deformation stage, and the plastic strain of the whole area remains at zero until plastic deformation begins in the α phase at B ( εT =0.0075). When the β phase also deforms plastically, C ( εT = 0.01) is the end point of the elastic to plastic stage. Point D ( εT = 0.05) is at the end of the simulation.
Fig.6. The plastic strain and Von Mises effective stress contours at points A ( εT = 0.005), B ( εT = 0.0075), and C ( εT = 0.01).
Comparing effective strain rates of three positions in the α grain along the selected path from A position near the phase boundary to the grain center (positions 1, 2,3). During elastic deformation, the effective strain rate of position 1 is ~2.5 ×10-5 s-1, and ~2.35 × 10-5 s-1 for positions 2 and 3. Position 1 has a relatively higher strain rate, so the strain leads that of other positions and the stress is more inclined to congregate near the phase boundary. Position 1 then enters primarily into the plastic deformation stage, and the strain rate increases to 3.2 × 10-5 s-1. Subsequently, stress release starts when positions 2 and 3 reach their critical yield stresses and also enter plastic deformation. The strain rates of positions 1 and 2 are influenced not only by the nearby β phase but also the stress transfer from the grain center position, which make them drop sharply with different levels. From their distances to grain center, the strain rates drop to 0.97 × 10-5 s-1 and 2.6 × 10-5 s-1, respectively. Therefore, the significant strain rate gradient inside α grain is the cause of the stress gradient. During plastic deformation, the effective strain rate evolutions of these positions first converge then separate with the consequence that position 1 has the highest value. It means that stress and strain will finally concentrate in the α phase particularly near the phase boundary. Thus, failure will initiate preferentially at these regions.
Fig.12. Effective strain rate evolutions of position 1 (near phase boundary), 2, and 3 (at grain center) in the α grain along the selected path.

Elastic plastic deformation of TC6 titanium alloy analyzed by in-situ synchrotron based X-ray diffraction and microstructure based finite element modeling
Journal of Alloys and Compounds 688 (2016) 787-795
文献10(2016): Determination of the single-phase constitutive relations of α/β dual phase TC6titaniumalloy(α/β双相TC6钛合金单相本构关系测定)
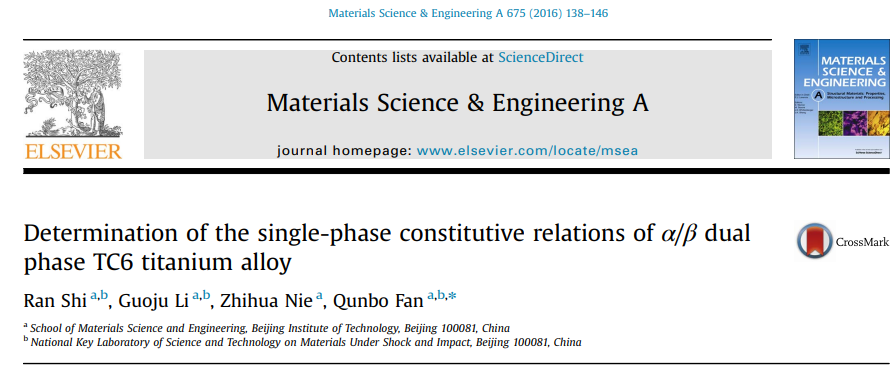
In the EPSC framework, the evolution of strain is determined for unidirectional strain loading in strain steps of 0.1%.Tocorrelate the orientation of single crystals with those on polycrystalline samples, crystallographic data are described by means of three Euler angles which are commonly used to describe the sample orientation relative to the crystal. For orientation measurements in Channel 5, the convention of Bunge is applied. The Euler angles: φ1,Φ,φ2 represent a rotation f φ1 about the z-axis, followed by a rotation of Φ about the rotated x-axis and followed by a rotation of φ2 about the rotated z-axis.Therefore, a set of discrete Euler angles of 6495 α grains and 2341 β grains are specified and weighted, based on the EBSD orientation distribution measurement. EBSD crystalline orientation maps (Inverse pole figures, IPFs) (Fig. 4) are colored according to the initial crystallographic orientation of each grain in the polycrystalline material paralleling to the LD of the sample within the coordinate system comprised by three important low-index axes.
Fig.4. Crystalline orientation maps of (a) α phase and(b)of β phase.
The SF frequency distributions of slip systems in the α grains(Fig. 5) increase from hard(i.e., lowest-SF,SF=0) orientations to soft(i.e.,highest-SF,SF=0.5) orientations. These four slip systems occur with frequencies of 61.98%, 55.06%, 84.18%,and 85.52%, respectively, in grains with SF values higher than 0.3. Plastic deformation occurs preferentially in high-SF grains. The orientations of these grains are referred to as favorably oriented components. Furthermore, with increasing deformation, the reorientation of deformed grains results in the rotation of unfavorably oriented grains to favorably oriented components. Sustainable plastic deformation of the α phase is initiated at a relatively large time scale.
Fig.5. Schmid factor maps and histograms of slip systems in the α grains: (a){0001}< 1120> basal, (b){1010}< 11..0> prismatic, (c){1011}< 1120> first-order pyramidal, and(d){1011}< 1123> second-order pyramidal slip systems.

Determination of the single-phase constitutive relations of α/β dual phase TC6titaniumalloy
Materials Science & Engineering A 675(2016)138–146
文献11(2010): High temperature deformation behavior of the TC6 titanium alloy under the uniform DC electric field(TC6钛合金在均匀直流电场作用下的高温变形行为)
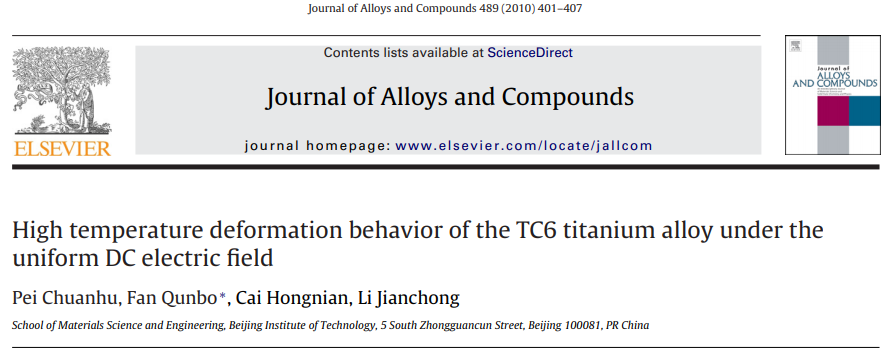
The microstructures of the fractured TC6 which are obtained by furnace cooling from 600℃, 700℃ and 800℃ to the room temperature, are shown in Figs.5, respectively. These microstructures can indirectly reflect the structure features of the TC6 during the stretching deformation process at the high temperature stage. Through these microstructures we can find obvious tensile deformation of the primary α phase and extraordinary uneven proportional distribution of the phases when the external electric field is not applied. However, at the same temperature more uniform distribution and finer secondary α phase precipitate from β phase when the external electric field is applied. As a result, these secondary α phase will relax the stress concentration and promote the coordination deformation of the grains. Obviously, the external electric field promotes the dynamic recrystallization of TC6 during the tensile process, homogenizing the distribution of second α phase, and retarding the partial growth of α grain thus coordinating the deformation of the grains at 600℃, 700℃ and 800℃. Form the above discussion, the conclusion can be reached that the ductility of TC6 are improved by the external electric field at 600℃, 700℃ and 800℃.
Fig. 5. Microscopic patterns of the TC6 at 600℃/700℃/800℃ under different electric field.

High temperature deformation behavior of the TC6 titanium alloy under the uniform DC electric field
Journal of Alloys and Compounds 489 (2010) 401–407

京公网安备 11010802033099号
京ICP备2020038205号-1