1953年,美国NASA-Lewis研究中心首次提出了热障涂层的概念,经过半个多世纪的不断发展,热障涂层材料在航空航天、石油化工、火力发电及核聚变反应堆等领域得到了广泛的运用。热障涂层材料体系是所有涂层体系中结构最复杂的,同时也是航空发动机内部高温零部件最急需应用的一种隔热涂层。目前实际使用的典型热障涂层材料体系主要包括四层:耐高温镍基合金基底、起过渡作用的粘结层、热生长氧化层和陶瓷层。 热障涂层作为一种极具优势的防护材料有着广阔的应用前景,但由于其自身结构的复杂性以及服役环境的恶劣性,涂层材料很容易在毫无征兆的情况下发生失效,甚至会引发特大安全事故并造成极大的经济损失。涂层的失效破坏长时间限制着热障涂层的应用领域,也成为了热障涂层进一步发展的瓶颈难题。因此,对热障涂层的失效分析和机理研究就显得尤为重要。
首页 >> 学术研究 >> 热障涂层
热障涂层
文献1(2015):Simulation of damage and failure processes of thermal barrier coatings subjected to a uniaxial tensile load(热障涂层在单向拉伸载荷作用下的损伤和失效过程的模拟)
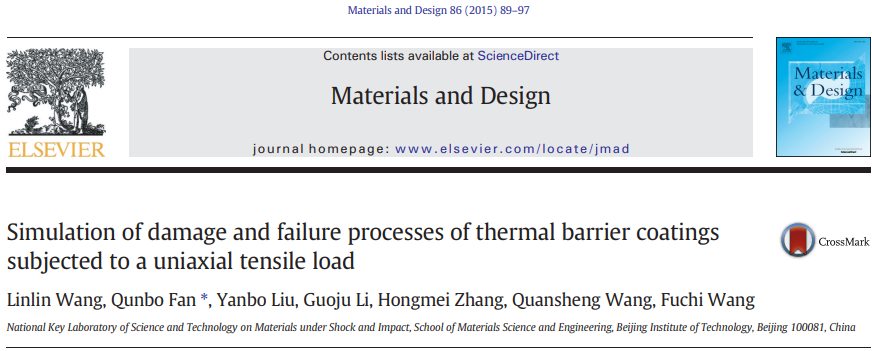
The geometrical shape of a selected section of the tested fracture surface (300.0×243.1μm) is represented by a 2D isometric image and a 3D topographical map, as shown in Fig. 9(a) and (b), respectively. The results show that the convex sections (labeled as “A”) correspond to the exposed bond coat, whereas the concave areas (labeled as “B”) correspond to the adherent top coat, and the difference in height between them is approximately 20–35μm.
Fig.9. Fracture morphology obtained by an optical profilograph: (a) 2D isometric image and (b) 3D topographical map.
The formation and propagation of the primary crack inside the top coat are shown in Fig. 14. At time t = 44.4 s from initial application of the load, the generated microcracks at the TC/BC interface [labeled as “I”, “II”, “III”, and “IV”, see Fig. 14(a)] propagate, amalgamate, and begin to form a primary crack, as shown in Fig. 14(b). This moment corresponds to the peak value of internal energy shown in Fig. 8. The inset in Fig. 14(b) displays the first principle stress vectors at the crack tip; tensile stress in the z-direction can be seen very clearly. As a result, the primary crack propagates horizontally inside the top coat along the interface direction, that is, normal to the vertical tensile stress. The specific crack propagation path is illustrated in Fig. 14(c).
Fig.14. Initiation and propagation of the primary crack: (a) microcracks at the TC/BC interface, (b) formation of the primary crack, and (c) propagation of the primary crack

Simulation of damage and failure processes of thermal barrier coatings subjected to a uniaxial tensile load
Materials and Design 86 (2015) 89–97
文献2(2015):Experimental Study and Numerical Simulation of the Tensile Test for GH4169 Coated with YSZ Coating at High Temperature(YSZ涂层的高温合金GH4169拉伸试验研究与数值模拟)
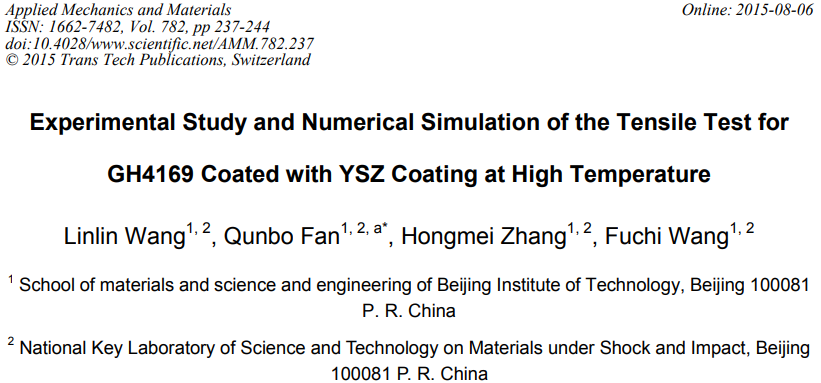
At time t=120s from initial application of the load, stress concentration mainly occurred in the YSZ ceramic top coating where the maximum tensile stress reached about 200 MPa. The maximum principal stress vectors at this moment show the presence of an axial stress of typical elements parallel to the loading direction, which is equally distributed through the thickness. Simultaneously, coating material was subjected to a radial stress (the intermediate principal stress which was much lower), which increased toward the interface between YSZ and bond coating, where the failure of coating was more liable to occur. As the applied load continued to increase, at t=180s, the maximum tensile stress eventually exceeded the tensile strength of YSZ, triggering severe debonding failure in the center region of the specimen.
Fig.5 The initial debonding failure of YSZ coating: (a) stress contours of the model at t=120s; (b) the maximum principal stress vectors inserted in Fig.5(a); (c) the intermediate principal stress vectors inserted in Fig.5(a); (d) coating delamination in the center region of the specimen.
Fig.7(a) shows the stress contours at t=780s, where it is seen that the residual coating can apparently change the stress distribution inside the metal substrate. The tensile stress of substrate with coating was nearly 40% lower than that without coating. Therefore, it can be concluded that YSZ coating can relieve stress significantly, thus helping prolong the substrate's service life in the same environment. As we can see from Fig. 7(b), residual YSZ coating near the interface was subjected to a vertical or oblique tensile stress, which induces further interfacial debonding failure, shown in Fig. 7(c). With the increase of external loading, at t=900s, only a few residues can be seen at the arc transitional region (Fig. 7(d)).
Fig.7 The final debonding failure of YSZ coating: (a) stress contours of the model at t=780s; (b) the maximum principal stress vectors inserted in Fig.7(a); (c) the interfacial debonding failure of the residual coating; (d) residues at the arc transitional region

Experimental Study and Numerical Simulation of the Tensile Test for GH4169 Coated with YSZ Coating at High Temperature
Applied Mechanics and Materials 782(2015)237-244
文献3(2013):Lifetime prediction of plasma-sprayed thermal barrier coating systems(等离子喷涂热障涂层系统的寿命预测)
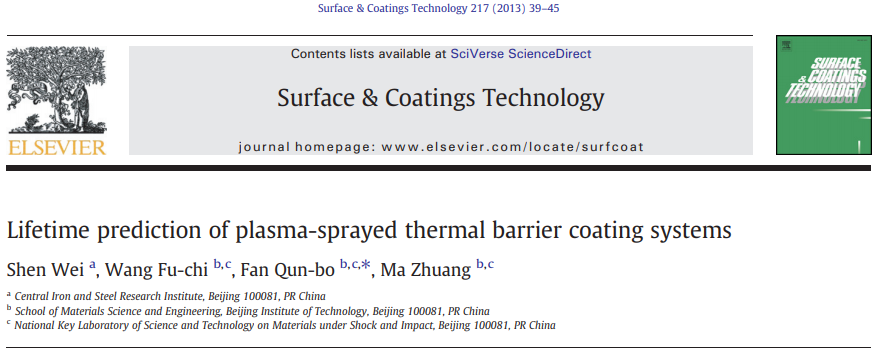
The growth of the TGO (thermally grown oxide) is an important phenomenon responsible for the spallation failure of TBC. During isothermal oxidation in Tmax, TGO forms and grows at the top coat/bond coat interface. A series of scanning electron microscopy (SEM) micrographs over 200 images at 2000 magnifications is taken to identify the TGO thicknesses for each statistical cycle number listed in Table 2. Fig. 2a–d shows typical SEM micrographs of TGO growth after different thermal cycles. Subsequently, the statistical method is used to identify the average thickness of TGO. It shows that the average thickness of the TGO is 1.62μm after 8 cycles. With thermal cycles and exposure time increasing, the TGO thickness increases. When thermal cycling increases to 850 cycles (850 hour exposure time), the average thickness of the TGO accumulation is up to 6.50μm, which is approximately fourfold over the thickness after 8 cycles.
Fig.2. Typical SEM micrographs of TBC after isothermal oxidation and thermal cycles revealing the growth of TGO. (a) 100 cycles; (b) 200 cycles; (c) 600 cycles; and (d) 850 cycles
Fig. 13 shows the 1st stress distribution in TC at room temperature during 900 cycles. The peak of 1st stress reaches 222 MPa in region C, where is the most vulnerable part in TBC. According with the simulation results, microcrack growth observed in the similar region where is away from macrocracks observed in the surface of TBC by naked eyes is shown in Fig. 14 after 850 cycles. During 810–900 cycles, the peak of 1st stresses in TC will reach the failure stress, hence, the lifetime of TBC is determined between 810 and 900 cycles with the TGO thickness between 6.4 and 6.6μm, which agrees with experimental average lifetime 860 cycles. Because the interface model with periodic boundary conditions is effectively modeled as infinite series of undulation morphological characteristics r(i), the TBC life predicted by FEM can reflect the experimental result effectively.
Fig.13. The maximum principal stresses in TC with 900 thermal cycles and Crack growth in similar region C.

Lifetime prediction of plasma-sprayed thermal barrier coating systems
Surface & Coatings Technology 217 (2013) 39–45
文献4(2012):Effects of defects on the effective thermal conductivity of thermal barrier coatings(缺陷对热障涂料有效导热系数的影响)
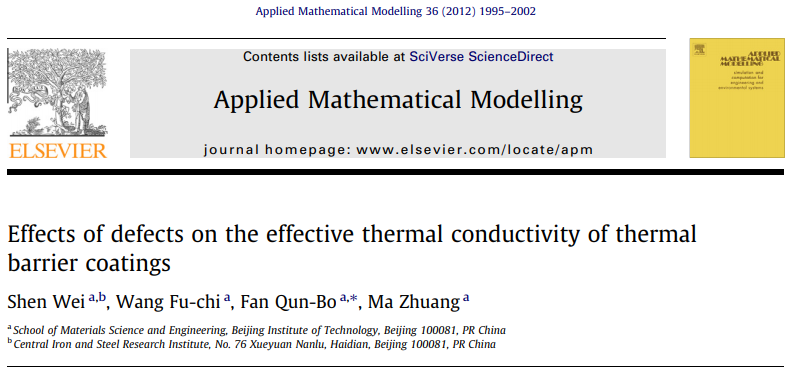
A typical microstructure of plasma sprayed TBCs from the cross-section view by scanning electron microscopy (SEM) is shown in Fig. 4. It includes yttria partially stabilized zirconia (YSZ) and defects. The model size is 120μm × 90μm within the total porosity fraction of 3.68%. A finite element grid model with more than 40,000 quadrilateral elements in Fig. 5a based on the actual microstructure of TBCs is generated by digital image processing theory and finite element mesh generation principle. The results indicated that the effect of the longest transverse crack is smaller than all the other defects combined together. However, the longest transverse crack still by all odds plays the most important role for the effective thermal conductivity of TBCs along the spray direction than any individual defect.
Fig.4. The cross-section microstructure of TBCs and the finite element grid model of TBCs with (a) all defects inside, CK = 1763μm2, D = 2160μm2. (b) only No.1 defect inside, CK (1) = 956μm2, D(1) = 956μm2.

Effects of defects on the effective thermal conductivity of thermal barrier coatings
Applied Mathematical Modelling 36 (2012) 1995–2002
文献5(2011):Finite element simulation of tensile bond strength of atmospheric plasma spraying thermal barrier coatings(气体等离子喷涂热障涂层抗拉结合强度的有限元模拟)
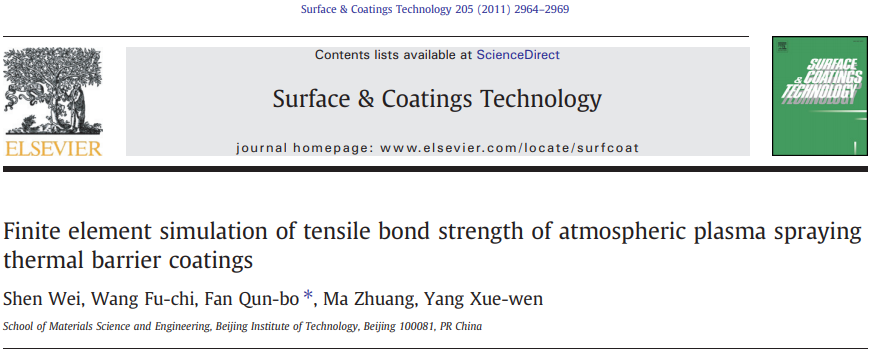
As is seen in Figure 5, the strain localization region is readily observed in the direction of 45 °, leading to the formation of the adiabatic shear band. When the α phase proportion outside the shear band is varied from 13.8%~46%, with the increase of the α phase proportion, the strain localization region decreases. For the α phase proportion of 13.8%, it has the largest strain localization region, the highest strain is more than 2.9, and the initiation of apparent cracks are observed; however, when the α phase proportion increases to 46%, the highest strain is lower than 0.7, and the strain localization region almost disappears. In order to further study the phenomenon, influence of the α phase proportion outside the shear band on adiabatic shear sensitivity is calculated. The results show that as the α phase proportion changes from 13.8% to 46%, the crack initiation time is varied from 40.1μs to 46.2μs, and the difference of crack initiation time is up to 6.1μs, which indicates the α phase proportion outside the shear band is the key factor that dominates the adiabatic shear sensitivity of equiaxed titanium alloys and the adiabatic shear sensitivity decreases with increasing α phase proportion within a certain proportion of α phase. The research further shows that since the α phase has a better uniform plastic deformation ability than the β phase has, with the increase of the α phase proportion, the uniform plastic deformation ability increases, resulting in a decreased tendency of strain localization, thus the adiabatic shear sensitivity decreases.
Fig.5.(a) Maximum tensile stress distribution in the beginning of crack growth. (b) Cracks growth at 33.2 s. (c) Cracks growth at 33.6 s. (d) Fracture at 34 s.
Sometimes, fracture even occurs in TC away from the interface, as shown in Fig. 6. The long transverse cracks in TC at or near TC/BC interface are found to be the most vulnerable parts of APS TBCs. When loads are gradually applied to a solid body, they will lead to the deformation of the material. Provided no energy is lost in the form of heat, the external work done by the loads will be converted into internal work called strain energy. When loads are gradually applied to TBCs, the strain energy goes up correspondingly. With increasing the load, the stress intensity at the crack tip rises until a threshold value and the crack grows uncontrollably. Meanwhile, a large number of elements satisfied with failure criterion are deleted from the model, and thus, the strain energy releases quickly.
Fig.6.(a) The cross-section microstructure of APS TBCs. (b) Simulation results of fracture

Finite element simulation of tensile bond strength of atmospheric plasma spraying thermal barrier coatings
Surface & Coatings Technology 205 (2011) 2964–2969
文献6(2010):Proposal of new expressions for effects of splat interfaces and defects on effective properties of thermal barrier coatings(溅射界面和缺陷对热障涂层有效性能影响新表达式的提出)
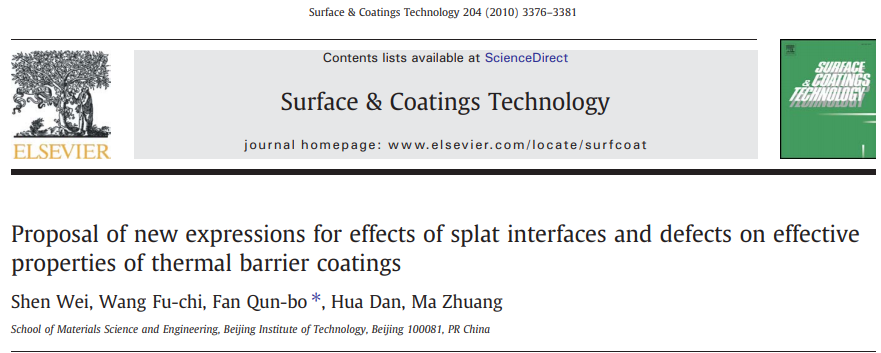
In this paper, over 200 images are selected and more than 70,000 quadrangle elements are used in each finite element mesh, as shown in Fig. 4(a) and (b). Fig. 4 shows distributions of stress in spray direction and thermal gradient under steady-state conditions, grey color represents normal regions (1± 20% σ0 or 1±20% ΔT/h) not affected by defects, while other colors indicate nonlinear stress region and thermal gradient region. In Fig. 4 (c) and (d), the stress contours and thermal gradient contours clearly illustrate the effects of defects. There are obvious concentrations of stress and thermal gradient around defects. Generally, higher stresses or thermal gradients contribute to lower effective Young's modulus or thermal conductivity. The Young's modulus and the thermal conductivity of the coating in the spray direction namely Ee and Ke are measured as 56 GPa and 1.08 W/mK, respectively.
Fig.4. Finite element model and distributions of stress and thermal gradient. (a) A SEM cross-section image of YSZ coating (212μm × 159μm). (b) Finite element model according with SEM image. (c) Stress profile. Grey color represents normal region (1 ± 20% σ0) not affected by defects, while other colors indicate nonlinear stress region Ω. (d) Thermal gradient profile. Grey color represents normal region (1 ± 20%ΔT/h) not affected by defects, while other colors indicate nonlinear thermal gradient region Ψ.
Three artificial finite element models with dimensions 25 μm×25 μm and more than 20,000 elements are designed in Fig. 5: all of the defects are idealized and assumed to be spheroid elements with the aspect ratios of b/ a=0.6 (a and b are major and minor axes, a=0.7 μm) in Fig. 5(a); all of the interfaces are idealized and assumed to be rectangle elements with the size of 3.25 μm×0.125 μm in Fig. 5(b); Fig. 5(c) shows the model containing defects and interfaces together. A comparison between effect coefficients of defects and splat interfaces, namely α and β, shows that the Young's modulus effect coefficient of splat interfaces is more than triplicate effect coefficients of defects, indicating that splat interfaces have much greater influences on the Young's modulus than defects. Comparing ϕ and φ it can be found that the splat interfaces makes more contribution than defects in defining the thermal conductivity of plasma sprayed Coatings.
Fig.5. Finite element models used to estimate effective properties and effect coefficients. (a) Idealized spheroid elements representing the defects in coatings. (b) Rectangle elements representing the splat interfaces in coatings. (c) The model containing defects and interfaces together.

Proposal of new expressions for effects of splat interfaces and defects on effective properties of thermal barrier coatings
Surface & Coatings Technology 204 (2010) 3376–3381
文献7(2010):基于数字图像处理技术的等离子喷涂氧化锆涂层热导率影响因素有限元研究(Finite Element Study of Influence Factors on Thermal Conductivity of Plasma Sprayed Zirconia Coatings Based on Digital Image Processing)
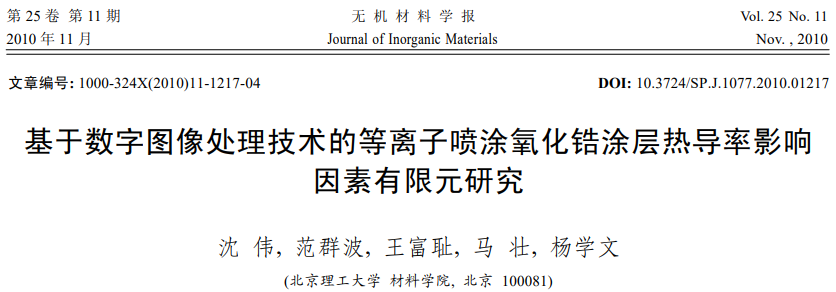
可通过灰度阈值分割技术识别涂层显微图像内部的陶瓷材料、孔洞及裂纹等。 灰度阈值分割是最常见的图像分割处理方法。图1(a)为氧化锆涂层SEM 照片,图中暗区代表了孔洞和裂纹,而亮区则表示陶瓷。将二元图像转化成矢量化的显微组织结构并导入有限元分析软件中,生成与涂层显微组织相一致的有限元模型, 如图1(c)所示,从而在氧化锆涂层隔热性能计算中考虑了材料的非均质性。
图1 涂层截面与有限元网格模型
图2(a)为涂层的温度梯度▽T分布云图。缺陷的存在一方面改变了温度梯度在涂层中的分布,使得在缺陷的周围存在明显的温度梯度集中区,从而有效地降低了涂层的热导率;另一方面,高的温度梯度也会导致高的应力区域的出现,降低了涂层的力学性能。图2(b)为涂层中的最大主应力分布图,深色区域为应力集中区,是陶瓷层中最薄弱的部分,当应力积累到一定程度时,裂纹会由此迅速扩展,并最终导致涂层失效。
图2 涂层温度梯度(a)与第一主应力(b)分布图
文献8(2010):基于涂层显微组织图片的拉伸实验有限元数值模拟(Finite Element Simulation of Virtual Tensile Experiment Based on Microstructural Images of Coating)
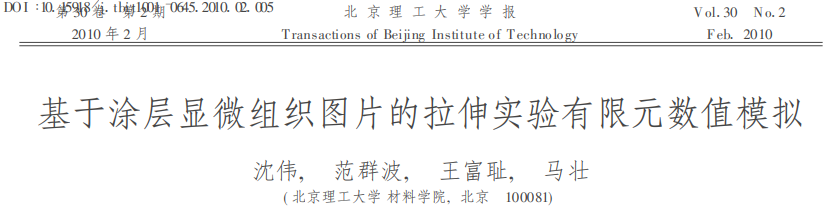
图5 为不同时刻的裂纹扩展图。t =46.8 s时,裂纹从A 点位置开始扩展,此时的拉应力载荷为78.0MPa;t =53.1 s时,横向裂纹贯穿整个模型,该区域内的涂层已被拉断,此时的拉应力载荷为88.5MPa。图6 表明,随着拉应力载荷不断增加,应力在裂纹尖端处迅速积累.当涂层内部应力达到失效应力时,首先从A 端点处裂纹开始迅速向左侧扩展;然后B 点和C 点处裂纹开始向右侧扩展,同时孔隙b 处裂纹开始向上纵向扩展;最终横向裂纹贯穿整个涂层,涂层被拉断裂纹的扩展方式以横向扩展为主,涂层最终断裂方式为层裂.裂纹扩展导致涂层失效的过程中,横向主裂纹α 起了主导作用,而纵向裂纹和孔洞的贡献很小。
图5 不同时刻裂纹扩展图
采用轴向拉伸法研究相同喷涂工艺得到TBCs的失效形式。图7为拉伸断裂ZrO2陶瓷层断口形貌图,在断口面上微裂纹较多,喷涂过程中形成的横向微裂纹是导致涂层失效的主要原因。实验表明,断裂发生在陶瓷层内部,断裂形式为层裂。实验结果与模拟结果基本一致。值得说明的是,由于实际涂层的拉伸断裂失效因素很多,除了ZrO2陶瓷层的显微组织形貌外,还受到涂层内部界面结合状态等因素的影响。
图7 拉伸断裂ZrO2 陶瓷层断口形貌图
文献9(2009):基于显微组织图片的涂层热导率有限元计算研究(Finite Element simulation of Thermal conductivity Based on Microstructural Images of Thermal Barrier Coatings)
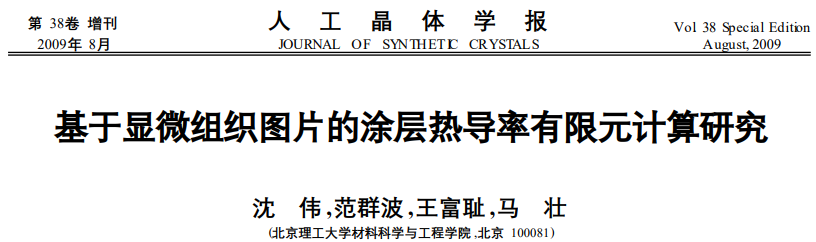
先通过扫描电子显微镜( SEM)得到ZrO2涂层横截面的局部位置放大物理图像文件,然后选取图像中某一特定区域,利用灰度阈值分割处理方法将整个图像分成2个部分,转化成一个二值图像。根据下面的算式,得到一个二值图像。随后根据不同的像素点灰度值对应着不同的材料组元,将像素点单元的集合转换成有限元网格单元的集合,建立得到网格单元数为125 ×100的有限元网格模型,大小为125μm ×100μm。
图1 ZrO2涂层横截面显微组织图像、灰度分割二值图及有限元网格模型
ZrO2涂层稳态温度场分布如图4所示。图4表明,由于孔洞、裂纹的存在及其分布的不均匀性,导致了涂层稳态温度场的分布也极不均匀。尤其在孔洞、裂纹附近,温度梯度相对较大。孔洞、裂纹等缺陷的存在影响了涂层热量的传递。孔隙的存在降低了涂层的有效热导率;等离子喷涂ZrO2涂层中沿喷涂方向较垂直喷涂方向具有更低的热导率,低的热导率决定了ZrO2涂层沿喷涂方向具有更优的隔热性能。分析ZrO2涂层图片的显微组织结构,裂纹分布以横向为主。裂纹的横向分布阻碍了热流的纵向传播,从而降低了涂层的纵向热导率,提高了涂层的隔热性能。涂层热导率受孔隙率和孔隙形状共同影响。
图4 ZrO2涂层稳态温度场分布图
文献10(2009):Modeling of micro-crack growth during thermal shock based on microstructural images of thermal barrier coatings(基于热障涂层微观结构图像的热冲击微裂纹扩展模拟)
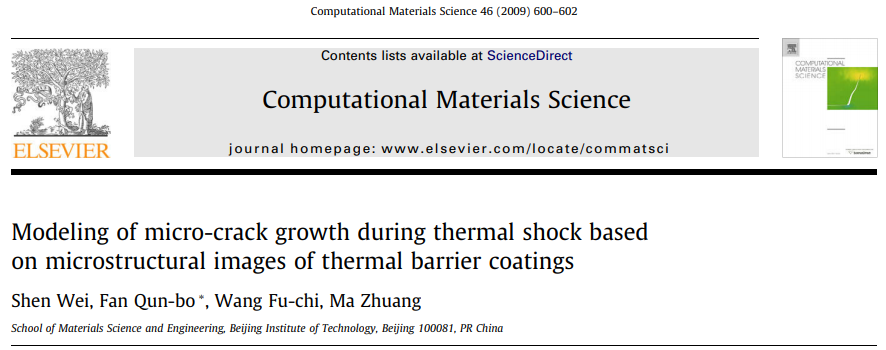
A typical microstructure of plasma sprayed TBCs from the cross-section view by scanning electron microscopy (SEM) is shown in Fig. 1. The model size is 240μm× 180μm. It includes YSZ TC and NiCoCrAlY BC with the dark color indicating defects of voids and micro-cracks. Such an image can be transferred to a digital image by digital image processing technology. A finite element grid model in Fig. 2 based on the actual microstructure of TBCs is generated by thresholding segmentation and finite element mesh generation principle. This finite element model is made up of 180 135 finite elements, and the dimensions are 240μm× 180μm.
Fig.1. The cross-section microstructure and the finite element grid model of TBCs
After 25 thermal shock cycles, the micro-crack growth caused by high temperature gradient and different CTE is shown in Fig. 3. Due to high temperature gradient and the existence of defects, the tensile stresses in the horizontal direction are induced during thermal shock, so vertical cracks initiated in the TC are developed, thus causing spallation of the TC finally. The presence of vertical cracks can relieve residual stress, thus enhance TBCs thermal shock resistance and prevent further delamination of TC. However, the large delamination crack in the TC makes it transparent to oxygen, and hence the thermally grown oxide (TGO) is easily formed at the interface of the TC and BC during high-temperature exposure. As shown in Figs. 3 and 4, a comparison between experimental results and numerical results shows that after 25 thermal shock cycles, the crack growth in simulation result agrees well with the corresponding experimental result. The methodology in our present work is effective to model the micro-crack growth.
Fig. 3. Simulation result and experimental result of micro-crack growth after 25 thermal shock cycles.

Modeling of micro-crack growth during thermal shock based on microstructural images of thermal barrier coatings
Computational Materials Science 46 (2009) 600–602
文献11(2009):Molecular dynamics calculation of thermal expansion coefficient of a series of rare-earth zirconates(稀土锆酸盐热膨胀系数的分子动力学计算)

Fig.3 shows the equilibrium-location deviations versus different potential energy differences relative to the ground state for Zr–O, O–O, and serial A–O bonds. Among these different atom pairs, or bonds, it is found that the Zr–O bond is the most important factor in determining the overall TECs of different pyrochlore zirconates, and the A–O bond plays a secondary role. However, O–O has little effect on the TECs.
Fig.3. Equilibrium-location deviations for different potential energy differences, relative to the ground state.
Fig.4 shows the pyrochlore structure and the fluorite structure of Er2Zr2O7. It can be seen that the minimum-length bond in the fluorite structure is the Zr–O bond, which at 2.2985 Å is longer than in the pyrochlore structure (2.0324 Å). The longer the bond is, the weaker the bond is. Correspondingly, the minimum-length bond of a crystal structure reflects the strongest bonding strength in the crystal structure. In addition, for the same chemical composition with different phase structures, the anharmonicity effects are approximately the same since the same set of potential parameters are used. In such a case, the weaker the bonding strength, the larger the TEC. So, bonding strength is another important factor that affects TECs. Therefore, the fluorite structure has a higher TEC.
Fig.4. Crystal structure of Er2Zr2O7.

Molecular dynamics calculation of thermal expansion coefficient of a series of rare-earth zirconates
Computational Materials Science 46 (2009) 716–719
文献12(2008):Prediction of the intrinsic thermal conductivity of phonons in dielectric and semiconductor materials based on the density of the lattice vibration energy(基于晶格振动能量密度预测介电和半导体材料中声子的本征热导率)
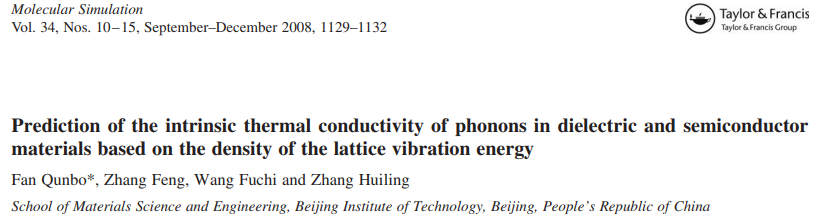
Figures2 show the phonon DOS of α-SiO2 and cubic ZrO2 (c-ZrO2), respectively. Based on the phonon DOS results, the heat capacity can be calculated from Equation (2), as shown in Figure 3. The agreement with experimental data is found to be good. A comparison between the calculated and experimental thermal conductivities shows that the calculated values of Si, α-SiO2, and La2Zr2O7 are reasonably good. Although there were some differences between the calculations and experiments for Ge and c-ZrO2, these were probably caused by the calculation of the phonon DOS, or phonon scatter effects due to various defects in the crystals. It is still a first-step methodology to calculate the intrinsic phonon thermal conductivity of perfect-crystal dielectric and semiconductor materials through theoretical calculation without the need to input any experimental data
Figure 2. Phonon DOS of a-SiO2 and cubic ZrO2.
Figure 3. Heat capacity of a-SiO2 and cubic c-ZrO2.

Prediction of the intrinsic thermal conductivity of phonons in dielectric and semiconductor materials based on the density of the lattice vibration energy
Molecular Simulation 34(2008):1129-1132
文献13(2008):Study of ZrO2 phase structure and electronic properties(ZrO2的相结构和电子性质的研究)
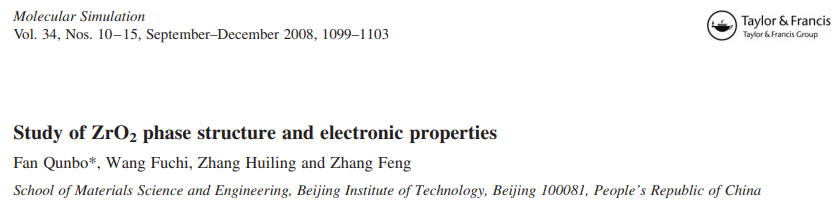
To compare the charge distribution characteristics for three ZrO2 polymorphs, the charge distribution on a typical plane is presented in Figures 6–8, respectively. Figure 6 shows the charge distribution on a typical c-ZrO2 plane with miller index (1 1 -2) and across the point (2.53, 2.53, 2.53); Figure 7 shows the charge distribution on a typical t-ZrO2 plane with miller indices (0 1 0) and across the point (1.82, 1.82, 2.64); and Figure 6 shows the charge distribution on a typical m-ZrO2 plane with miller indices (20.68 0.68 20.27) and across the point (2.48, 2.56, 2.20). As shown in these figures, the maximum charge density for c-ZrO2, t-ZrO2 and m-ZrO2 is 5.098, 7.234 and 7.261 electrons/ Å3, respectively, which is agreement with phase stability tendency at ground state. Namely, the larger the maximum charge density is, the stronger the bonding strength is, and the more stable the phase is.
Fig.6. Charge distribution on a typical plane of c-ZrO2 and t-ZrO2 and m-ZrO2

Study of ZrO2 phase structure and electronic properties
Molecular Simulation 34(2008):1099-1103
文献14(2008):Splat Formation of Plasma Sprayed Functionally Graded YSZ/NiCrCoAlY Thermal Barrier Coatings(等离子喷涂功能分级的YSZ/NiCrCoAlY热障涂层的溅射形成)

Fig.1 shows the splat formation SEM photographs of varying mass fractions of YSZ and NiCrCoAlY deposited by plasma spray process parameters shown in Tab.1. According to the Tab.1, when increasing the ratio of YSZ by 20 percent, increasing I and FHe and decreasing FAr, YSZ powder melt better, as seen in the Fig. 1. A relatively complete ball YSZ powder can be seen (shown in Fig.1a) and the size of YSZ powder un-melted is big. The size of un-melted one in 40% YSZ /60% NiCrCoAlY gets smaller (shown in Fig.1b) and its shape is quite different from original ball powder. Likewise, Fig.1c shows that size of un-melted YSZ powder in 60% YSZ /40% NiCrCoAlY get further smaller and even certain big size original YSZ powder melts totally. Splat formation morphology of 80% YSZ /20% NiCrCoAlY is similar to that of 60% YSZ /40% NiCrCoAlY, as shown in Fig.1d. Original YSZ powder that can melt totally is much bigger than that shown in Fig.1c.
Fig.1 Splat morphology of ZrO2/NiCrCoAlY
Fig.2 shows the results of the corresponding plasma jet temperature fields mentioned above in Fig. 1. The horizontal X axis stands for distance from one position on gun axis to gun exit and the vertical Y axis stands for plasma jet temperature (T). The temperature at gun exit is defined as T0. With respect to Fig.2a-d, T0 demonstrates the increasing tendency in spray process parameters in Tab.1, which reaches individually 8890K, 10500K, 10900K and 12300K. Furthermore, the same tendency appears at each value along X axis. In conclusion, increasing I and FHe and decreasing FAr, T takes on an increasing tendency. In hotter plasma jet background, thermal conductivity from jet to powder is so effective that powder melts better and splat spreads more easily.
Fig.2 Plasma jet temperature field by the four process parameters in Tab.1. (a) I=600A, FAr=120SCFH, FHe=15SCFH; (b) I=700A, FAr=110SCFH, FHe=15SCFH; (c) I=700A, FAr=100SCFH, FHe=25SCFH; (d) I=800A, FAr=85SCFH, FHe=315SCFH

Splat Formation of Plasma Sprayed Functionally Graded YSZ/NiCrCoAlY Thermal Barrier Coatings
Key Engineering Materials 368-372(2008)1862-1865
文献15(2008):Perturbation Molecular Dynamics Simulation of Thermal Conductivity of Zirconia(氧化锆热导率的微扰分子动力学模拟)
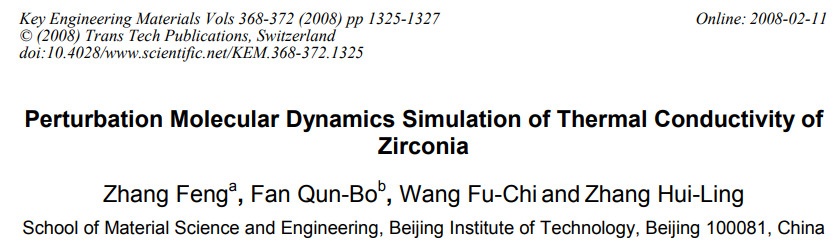
Fig.2 shows the calculated thermal conductivity for ZrO2 and YSZ. It can be seen that the significant decrease in thermal conductivity caused by Y2O3 addition. In addition, it’s found that with increasing the temperature, the thermal conductivity always decreases both for ZrO2 and for YSZ. After taking photon conductivity into account, shown in Fig.3, thermal conductivity at temperatures higher than 1200K is found to be rising, instead of always decreasing to a certain value, which successfully reproduces the experimental observations. By contrasting calculated thermal conductivity and experimental ones reported by literatures, it can be found that the calculated values are relatively higher.
Fig.2 Phonon thermal conductivity of ZrO2 and YSZ(a)before and (b)after taking photon conductivity into account
Fig.4 shows instantaneous lattice constant of ZrO2 as a function of temperature. It can be seen that the instantaneous lattice constant fluctuates around a line which was fit to describe the theoretical relation between lattice constant and temperature. Linear thermal expansion coefficient of a material can be calculated by dividing the slope of the fit line with the initial lattice constant. Calculated and experimental values are compared in Table 2. It can be seen that the calculated results are smaller than the experimental ones. But the increment of thermal expansion coefficient caused by Y2O3 addition is reproduced well. In spite of possible calculation errors for thermal expansion coefficient, the method proposed in this paper is still acceptable.
Fig.4 Instantaneous lattice constant of ZrO2 as a function of temperature

Perturbation Molecular Dynamics Simulation of Thermal Conductivity of Zirconia
Key Engineering Materials 368-372(2008)1325-1327
文献16(2007):稀土锆酸盐焦绿石相结构的第一原理计算(First-principle calculations of rare earth Pyrozirconate structure)
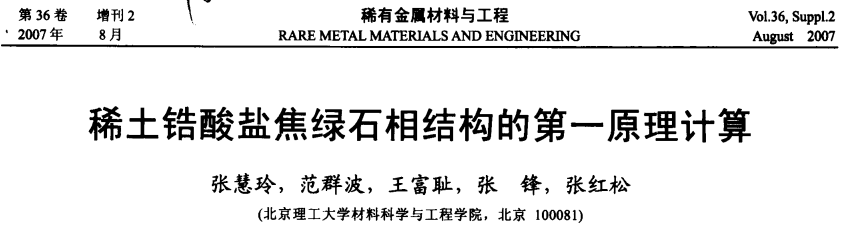
Mulliken键集居数是反映原子间作用力的有效工具,从 Mulliken集居数的计算结果(图5)可以看出在各稀土锆酸盐焦绿石结构中Zr-O键最强,Ln-O较弱,LnO最弱,该现象是O48f偏移引起键长畸变的结果。随着原子序数的增加Zr-O键有所减弱,说明其受到x增大的影响;Ln-O’键则有明显增强,说明其受到晶格收缩的影响。而键强最小的Ln-O键变化则较复杂,它并未因为晶格收缩,及x的增大而明显增强。
图5 键集居数随A位原子序数变化
本研究通过计算焦虑石结构的粉末XRD图谱,并与实际粉末的XRD实验结果进行比较进一步验证结构计算的准确性。图6为Sm2Zr2O7粉末的XRD图谱,可以看出,本文计算出的结构与实际粉末十分吻合,不仅衍射峰位置一一对应,而且峰强与轮廓也较准确。最强峰位于2915°,焦绿石的5个特征峰分别在14.45°、27.90°、36.95°、44.35°、50.90°。
图6 焦绿石相Sm2Zr2O7粉末XRD计算、实验结果比较
文献17(2007):功能梯度热障涂层隔热与应力缓和的组合设计(Integration design of heat insulation and stress relaxation for FGM thermal barrier coatings)
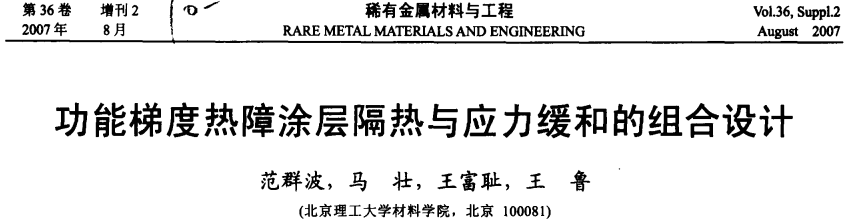
图6为不同层数的功能梯度材料径向热应力沿轴向位置的变化曲线。由图可知,材料径向热应力轮廓呈锯齿状且应力峰值在梯度层界面附近。3层材料的最大径向拉应力值为167MPa,远远大于5层材料44MPa,当材料层数大于5层时,随着层数的增加,径向热应力变化渐渐趋于平滑,界面处应力集中情况得到缓和。
图6 径向热应力沿轴向变化曲线
图7为轴向热应力沿轴向位置的变化曲线,变化趋势与径向应力类似。材料轴向热应力轮廓呈锯齿状且应力峰值出现在梯度层界面附近。随着材料层数的增加,轴向应力显著降低,5层材料的最大拉应力(56MPa)仅为3层材料(275MPa)的20%。
图7 轴向热应力沿轴向变化曲线

京公网安备 11010802033099号
京ICP备2020038205号-1